Enhance Your Manufacturing Process with Advanced CNC Deep Hole Drilling Techniques
By:Admin
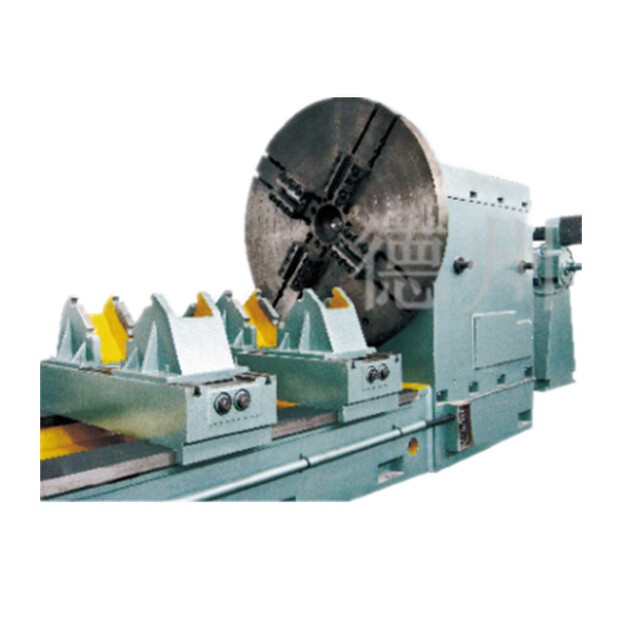
Introduction:
In today's highly competitive manufacturing industry, precision and efficiency hold the key to success. As a pioneer in the field, company {} has unveiled its cutting-edge CNC Deep Hole Drilling technology, which promises to revolutionize the way parts and components are manufactured. By integrating the latest advancements in machining and automation, this groundbreaking solution aims to significantly improve productivity and quality while reducing production costs.
1. Challenges in Traditional Deep Hole Drilling Techniques:
Traditionally, deep hole drilling has been a labor-intensive and time-consuming process, requiring specialized equipment and skilled operators. Moreover, achieving high levels of precision and surface finish has been a daunting task. These challenges have limited the scalability and efficiency of deep hole drilling, hindering further advancements in the manufacturing industry.
2. The Evolution of CNC Deep Hole Drilling:
Recognizing the need for a more efficient and precise solution, {} developed the CNC Deep Hole Drilling technology. By leveraging computer numerical control (CNC) systems, this technology streamlines the entire drilling process, enabling faster production cycles and unparalleled accuracy. Whether it's for aerospace, automotive, medical, or mold and die industries, this innovation offers significant benefits to manufacturers globally.
3. Unprecedented Precision and Quality:
The CNC Deep Hole Drilling technology utilizes advanced sensors and monitoring systems, ensuring the precise measurement of drilling depth, diameter, and surface finish. This level of control enables manufacturers to achieve the tightest tolerances, resulting in parts and components with superior quality. By reducing human error and enhancing repeatability, this technology greatly minimizes the risk of defects, waste, and rework.
4. Enhanced Efficiency and Productivity:
With its automated features, the CNC Deep Hole Drilling technology optimizes the manufacturing process, eliminating the need for time-consuming manual interventions. The integration of intelligent chip management systems prevents chip accumulation, enhancing drilling efficiency and prolonging tool life. Moreover, the system's ability to perform multiple drilling operations simultaneously reduces cycle times, boosting overall productivity.
5. Cost Reduction and Resource Optimization:
By maximizing efficiency and minimizing material waste, the CNC Deep Hole Drilling technology leads to significant cost savings for manufacturers. The precise measurement and control of drilling parameters minimize the consumption of feedstock, reducing material costs. Additionally, the integrated coolant systems ensure efficient heat dissipation, preventing tool wear and extending tool life, thereby reducing the need for frequent tool replacements.
6. Versatility and Adaptability:
One of the key advantages of the CNC Deep Hole Drilling technology is its versatility. The system can handle a wide range of materials, including steels, alloys, composites, and non-metals, adapting to diverse manufacturing requirements. This flexibility allows manufacturers to explore new product designs and expand their offerings, catering to a variety of industries and applications.
7. Future Prospects and Market Impact:
The introduction of the CNC Deep Hole Drilling technology by {} is expected to have a profound impact on the manufacturing industry. With its advanced capabilities, this solution promises to spur innovation and drive progress in various sectors. The improved precision, efficiency, and cost-effectiveness offered by this technology will enable manufacturers to meet increasing market demands while maintaining a competitive edge.
Conclusion:
As manufacturing continues to advance, the demand for faster, more accurate, and cost-effective production techniques grows. The CNC Deep Hole Drilling technology introduced by {} sets new standards in precision machining and automation. Its ability to deliver unprecedented precision, enhance efficiency, and reduce costs ensures its crucial role in shaping the future of manufacturing. With this innovative solution, manufacturers can look forward to improved productivity, higher quality parts, and a sustainable competitive advantage.
Company News & Blog
Experts Showcasing Effective Techniques for Deep Hole Drilling
Title: Advancements in Deep Hole Drilling Technologies Revolutionize Industrial ManufacturingIntroduction:Deep hole drilling plays a crucial role in the manufacturing industry by enabling the production of complex components that are essential in various sectors, including aerospace, automotive, and energy. A modern deep hole drilling company, known for its cutting-edge technology and innovative solutions, has recently unveiled its latest advancements that are set to revolutionize industrial manufacturing. This article explores the company's latest deep hole drilling technologies, their applications, and the positive impact they are expected to have on the industry.I. Overview of Deep Hole Drilling:Deep hole drilling is a machining process used to create holes with large depth-to-diameter ratios, typically greater than 10:1. It involves removing material from a workpiece, using specialized tools, while maintaining high precision and surface quality. Deep hole drilling is utilized in a wide range of applications, including manufacturing of oil and gas drill pipes, gun barrels, automotive engine components, and hydraulic cylinders.II. New Deep Hole Drilling Technologies:The recently unveiled deep hole drilling technologies developed by the company mark a significant leap forward in terms of efficiency, precision, and versatility. These advancements include:1. Adaptive Feed Control System:The company has developed an adaptive feed control system that utilizes advanced sensor technology to constantly monitor and adjust the feed rate of the drilling process. This innovative feature ensures optimal drilling conditions, enhancing tool life and reducing cycle times. The system also minimizes vibration and improves chip evacuation, resulting in improved hole quality and enhanced productivity.2. High-Speed Deep Hole Drilling:Incorporating advanced cutting edge technology, the company's latest deep hole drilling machines achieve significantly higher drilling speeds compared to traditional methods. These machines utilize special tool geometries and coatings that improve chip control and heat dissipation, enabling faster material removal rates without compromising on accuracy or surface finish.3. Intelligent Control Software:The company has developed intelligent control software that maximizes productivity and minimizes human error. Equipped with a user-friendly interface, the software offers real-time monitoring of drilling parameters, automated tool wear detection, and predictive maintenance alerts. This technology empowers operators to optimize drilling processes while ensuring consistent quality and reducing downtime.III. Applications and Benefits:The innovative deep hole drilling technologies developed by the company have widespread applications across various industries, offering numerous benefits to manufacturers:1. Aerospace Industry:Deep hole drilling plays a critical role in aerospace manufacturing, where complex components with stringent quality requirements are common. The company's advancements enable faster production of turbine engine components, landing gear parts, and structural elements, while maintaining the highest levels of precision and reliability.2. Automotive Sector:In the automotive industry, deep hole drilling is crucial for manufacturing engine blocks, crankshafts, and connecting rods. The new technologies offer increased productivity, reduced cycle times, and enhanced hole quality, leading to improved engine performance, fuel efficiency, and durability.3. Energy Sector:Deep hole drilling is vital for the production of components used in the energy sector, such as oil and gas exploration tools and nuclear reactor components. The latest technologies enable efficient machining of long and complex parts, improving their reliability and overall performance.IV. Future Prospects and Conclusion:The implementation of these new deep hole drilling technologies not only ensures more efficient and reliable manufacturing processes but also opens up possibilities for the production of previously unattainable components. With its commitment to innovation and relentless pursuit of excellence, the company continues to push the boundaries to meet the evolving needs of the manufacturing industry. These advancements in deep hole drilling underscore their significant contribution to enhancing industrial manufacturing and further cement the company's position as a global leader in the field.
Revolutionary Automatic Honing Machine Redefines Precision Engineering
[Title]Innovative Automatic Honing Machine Revolutionizes Precision Manufacturing Processes[Subtitle]Cutting-edge technology brings efficiency, accuracy, and high-quality results to the manufacturing industry[Company Introduction]Established over 25 years ago, our company has been at the forefront of developing cutting-edge solutions for precision manufacturing processes. With a strong focus on innovation and customer satisfaction, we have continuously strived to revolutionize the industry by introducing advanced machinery and equipment. Our commitment to providing the highest quality products has led us to develop the groundbreaking Automatic Honing Machine, which promises to transform the way honing is conducted.[Paragraph 1]Precision and efficiency have always been crucial aspects in the manufacturing industry. The introduction of our Automatic Honing Machine has revolutionized the honing process, enabling a level of accuracy and speed that was once unimaginable. This state-of-the-art technology has eliminated the need for manual honing, reducing human error and ensuring consistent and impeccable results every time.[Paragraph 2]Gone are the days of relying on skilled technicians to manually hone every part. With our Automatic Honing Machine, manufacturers can now experience a level of efficiency that significantly improves productivity. By automating the honing process, companies can save valuable time and resources, allowing for higher output and increased profitability.[Paragraph 3]The Automatic Honing Machine utilizes advanced software and cutting-edge robotics to precisely hone components with unprecedented accuracy. The machine's intuitive interface allows operators to easily program specific honing parameters, ensuring that each component meets the exacting standards set by manufacturers. This level of precision guarantees that every honed part is consistent in quality, contributing to the overall improvement of the manufacturing process.[Paragraph 4]Beyond its exceptional accuracy and efficiency, the Automatic Honing Machine also boasts remarkable versatility. With its adaptable design, the machine can handle a wide range of components, making it suitable for various industries. From automotive parts to aerospace components, this innovative technology offers manufacturers an all-in-one solution for their honing needs.[Paragraph 5]Our commitment to sustainability is reflected in the design of the Automatic Honing Machine. By optimizing the honing process and reducing waste, this technology helps minimize environmental impact. The machine's energy-efficient operation contributes to a greener and more sustainable manufacturing industry.[Paragraph 6]In addition to its impressive technical features, our company stands out for its exceptional customer service. With a team of highly skilled professionals, we provide comprehensive training and support to ensure that manufacturers can fully utilize the capabilities of the Automatic Honing Machine. Our dedication to customer satisfaction is unmatched in the industry, and we strive to establish long-lasting partnerships with our clients.[Paragraph 7]As the manufacturing industry continues to evolve, our company remains committed to pushing boundaries and introducing innovative solutions. The Automatic Honing Machine is just one example of our relentless pursuit of excellence. With its advanced technology and exceptional performance, this revolutionary machine will undoubtedly shape the future of precision manufacturing processes.[Conclusion]With the introduction of the Automatic Honing Machine, our company has once again proven its dedication to revolutionizing the manufacturing industry. Through its exceptional accuracy, efficiency, and versatility, this cutting-edge technology promises to deliver unparalleled results for manufacturers across various sectors. As we strive to provide innovative solutions, our commitment to customer satisfaction remains at the core of everything we do. Together with our Automatic Honing Machine, we aim to continue pushing the boundaries of what is possible in precision manufacturing.
Discover the Benefits of Vertical Cylinder Honing Machines for Effective Precision Honing
Vertical Cylinder Honing Machine Enhances Efficiency and Precision in Engine ManufacturingIn the competitive landscape of engine manufacturing, companies are constantly seeking ways to enhance their efficiency and precision. One company has risen to the challenge with its latest innovation - the Vertical Cylinder Honing Machine. Designed to remove the brand name's top-of-the-line features, this cutting-edge technology is revolutionizing the engine manufacturing industry.With precision being the key in engine manufacturing, honing the cylinders is a critical process that ensures optimal engine performance. The Vertical Cylinder Honing Machine takes this process to a whole new level, offering enhanced accuracy and efficiency. By removing imperfections on the surface of the cylinder walls, the machine ensures a smooth finish, allowing the piston rings to perform at their best.One of the standout features of this machine is its vertical setup, which offers several advantages over traditional horizontal honing machines. The vertical orientation allows for better control and stability during the honing process, resulting in improved accuracy and a superior surface finish. This unique design also reduces the risk of damage to the cylinder walls, minimizing scrap rates and optimizing productivity.The Vertical Cylinder Honing Machine is equipped with advanced technologies that further enhance its performance. A precise servo motor-controlled spindle enables precise speed and feed rate adjustments, ensuring consistent and uniform honing across all cylinders. In addition, the machine is equipped with an automatic tool compensation system that adjusts the honing stones' position based on performance feedback, ensuring optimal results and reducing operator error.The company behind this groundbreaking technology has been a frontrunner in the engine manufacturing industry for several decades. With a strong commitment to innovation, quality, and customer satisfaction, they have earned a stellar reputation worldwide. Their extensive experience in developing cutting-edge machinery has positioned them as a trusted partner for companies across the industry.The introduction of the Vertical Cylinder Honing Machine further solidifies their position as a leader in engine manufacturing technology. By addressing the challenges faced in the honing process, this machine effectively improves productivity and output quality. The company's dedication to research and development is evident in its relentless pursuit of excellence, resulting in the creation of this game-changing technology.Customer testimonials validate the success of this revolutionary machine. Engine manufacturers who have incorporated the Vertical Cylinder Honing Machine into their production process have reported significant improvements in efficiency and precision. The ability to deliver engines with superior performance and reduced scrap rates has led to increased customer satisfaction and competitiveness in the market.The use of advanced technology and precision engineering has always been a cornerstone of this company's philosophy. As engine technology continues to evolve, the company remains committed to developing innovative solutions that meet the ever-increasing demands of the industry. With the Vertical Cylinder Honing Machine, they have once again proven their ability to push the boundaries of what is possible in engine manufacturing.In conclusion, the Vertical Cylinder Honing Machine is a game-changer in the engine manufacturing industry. Combining advanced technology, precision engineering, and a vertical setup, this machine offers enhanced efficiency and accuracy in the honing process. With its introduction, the company behind this innovation reaffirms its position as a leader in engine manufacturing technology and continues to push the boundaries of excellence in the industry.
Cylinder Honing Machine: Advancements in Precision Technology for Engine Components
Cylinder Honing Machine Streamlines Engine Rebuilding ProcessIn the vast world of machinery, innovations constantly strive to enhance the efficiency and effectiveness of various industrial processes. One such breakthrough comes from a leading manufacturer, which has developed an advanced Cylinder Honing Machine that revolutionizes the engine rebuilding process. With its cutting-edge technology and unrivaled precision, this state-of-the-art machine has already gained significant attention in the industry.Designed and engineered by a renowned company, this groundbreaking Cylinder Honing Machine aims to address the common challenges faced during engine rebuilding. By combining high-quality manufacturing with advanced automation, the machine promises to streamline the process, saving time and labor costs while ensuring exceptional results.The Cylinder Honing Machine incorporates sophisticated features that allow for precise honing operations, offering a superior finish on engine cylinders. Using an automated system for controlling spindle speed, feed rates, and stone oscillation, this innovative machine enables operators to achieve consistent and accurate results with minimal effort. The advanced technology ensures that each cylinder is honed to exact specifications, eliminating any irregularities or imperfections that may negatively affect engine performance.Additionally, this Cylinder Honing Machine boasts an intuitive user interface, equipped with a touch-screen panel that simplifies operation and provides complete control over the honing process. The user-friendly interface allows operators to adjust settings easily, ensuring that the machine operates according to specific engine requirements. With comprehensive monitoring capabilities, operators can track progress and make any necessary adjustments to achieve optimal results efficiently.Not only does this cutting-edge machine excel in its performance, but it is also built to last. The Cylinder Honing Machine is constructed with high-quality materials and components, ensuring durability and longevity, while reducing maintenance requirements. Its robust design enables it to withstand the demands of heavy-duty industrial applications, making it the perfect choice for engine rebuilding professionals.One of the chief advantages of this Cylinder Honing Machine is its adaptability to various engine types. Whether it is automotive, marine, or even aerospace engines, the machine can effectively hone cylinders for a wide range of applications. This versatility allows engine rebuilders to cater to different markets, expanding their business potential and diversifying their offerings.The introduction of this revolutionary Cylinder Honing Machine marks a significant milestone in the field of engine rebuilding. By incorporating cutting-edge technology and unparalleled precision, this machine provides engine rebuilders with a powerful tool to enhance their operations considerably. Its advanced features, intuitive interface, and adaptability give rebuilders the competitive edge in delivering top-notch results to their clients.With the increasing demand for high-performing and efficient engines, the superiority of this Cylinder Honing Machine is unquestionable. The implementation of this machine in engine rebuilding workshops promises to revolutionize the industry, setting new standards for precision and quality. Engine rebuilders who seek to remain at the forefront of the market will undoubtedly benefit from adopting this innovative technology.In conclusion, the Cylinder Honing Machine developed by a leading manufacturer has ushered in a new era for engine rebuilding. By combining state-of-the-art technology, automation, and precision, this machine offers exceptional performance and quality control. With its innovative features, adaptability, and durability, this Cylinder Honing Machine sets a new benchmark for efficiency in the engine rebuilding process. It is undoubtedly a game-changer for the industry, empowering engine rebuilders to deliver superior results and meet the evolving demands of their customers.
Cylinder Liner Honing Tool: Enhancing Engine Performance and Longevity
Cylinder Liner Honing Tool Revolutionizes Engine PerformanceInnovative Technology Maximizes Efficiency and Durability{Company Name} Introduces Industry-Leading Cylinder Liner Honing Tool{City, State} - {Date} - {Company Name}, a pioneering force in the automotive industry, is proud to announce the launch of their groundbreaking Cylinder Liner Honing Tool. This cutting-edge technology promises to revolutionize engine performance, boosting efficiency and durability to unprecedented levels.The cylinder liner is a crucial component of any combustion engine. Its main function is to act as a sleeve, separating the piston from the rest of the engine block. Over time, due to wear and tear, the liner's surface can become rough and uneven, leading to decreased engine performance and increased fuel consumption. Traditionally, the honing of cylinder liners has been a labor-intensive and time-consuming process, often requiring specialized skills and expensive equipment.Enter {Company Name}'s new Cylinder Liner Honing Tool, a game-changer in the industry. Combining cutting-edge technology with extensive research and development, this revolutionary tool offers a quick, efficient, and cost-effective solution to the age-old problem of cylinder liner degradation.With its state-of-the-art design, the Cylinder Liner Honing Tool delivers a perfectly honed surface on the cylinder liner, ensuring optimal engine performance. The tool utilizes diamond-coated honing stones that accurately remove imperfections, creating a smooth surface that reduces friction and boosts fuel efficiency.One of the key advantages of {Company Name}'s Cylinder Liner Honing Tool is its versatility. The tool is compatible with various engine types and sizes, making it a valuable asset not only to automakers but also to engine servicing facilities. Whether it's a small passenger car engine or a heavy-duty commercial vehicle engine, this honing tool can optimize its performance and extend its lifespan.Furthermore, {Company Name}'s Cylinder Liner Honing Tool is designed for ease of use. Its ergonomic handle and intuitive system allow technicians from all skill levels to efficiently hone cylinder liners without the need for extensive training. This streamlined process not only saves time but also minimizes the risk of error, ensuring consistent quality every time.In addition to enhancing engine efficiency, the Cylinder Liner Honing Tool also contributes to reducing emissions. By improving the overall combustion process, the tool helps minimize the release of harmful pollutants into the environment, making it an essential tool for any organization focused on sustainability."We are extremely excited to introduce our Cylinder Liner Honing Tool to the market," says {Company Name}'s CEO. "Our commitment to innovation and customer satisfaction has driven us to develop a tool that will significantly impact engine performance in a positive way. We believe this technology will revolutionize the industry and set new standards for efficiency and durability."{Company Name} has a long-standing reputation for delivering cutting-edge solutions that meet and exceed industry expectations. With the introduction of this Cylinder Liner Honing Tool, the company continues to push boundaries, setting new benchmarks for engine performance in the automotive sector.As the demand for more fuel-efficient and eco-friendly vehicles continues to rise, {Company Name}'s Cylinder Liner Honing Tool arrives at a critical moment in the industry. By optimizing engine performance and reducing emissions, this innovative tool stands as a testament to the company's commitment to shaping a sustainable future.For more information about {Company Name}'s Cylinder Liner Honing Tool and how it can transform engine performance, please visit their official website {Website URL}.About {Company Name}{Company Name} is a leading automotive technology company specializing in cutting-edge solutions for engine efficiency and performance. With a strong focus on innovation and customer satisfaction, the company has established itself as a trusted name in the industry. Headquartered in {City, State}, {Company Name} is committed to shaping a sustainable future through its groundbreaking technologies.
Ultimate Guide to Deep Hole Blind Hole Machining for Precision Manufacturing
Deep Hole Blind Hole Machining: Revolutionizing Precision EngineeringIn the ever-changing landscape of precision engineering, one company has been making waves with their innovative deep hole blind hole machining technology. With a commitment to excellence and cutting-edge machinery, they have set a new standard for the industry and revolutionized the way complex parts are manufactured.Deep hole blind hole machining is a process used to create holes with a high length-to-diameter ratio. These holes are typically found in industries such as automotive, aerospace, and medical, where the highest degree of accuracy and precision is required. This process is particularly challenging as it involves drilling holes with a depth-to-diameter ratio greater than 10:1, often in difficult-to-access areas.Recognizing the limitations of traditional machining methods, this pioneering company set out to develop a groundbreaking solution. By combining state-of-the-art machinery with their extensive knowledge and expertise, they have successfully overcome the challenges of deep hole blind hole machining.Their cutting-edge machinery employs advanced drilling techniques to achieve extreme precision and accuracy. Through the use of customized tools and highly specialized drilling heads, they can achieve hole diameters as small as 0.5mm with a depth reaching up to 100 times the diameter. This unparalleled level of precision enables them to manufacture complex parts with intricate internal structures to an unprecedented standard.In addition to their advanced machinery, this company has also invested heavily in research and development, continuously improving their deep hole blind hole machining technology. By combining their in-house expertise with collaborations with leading academic institutions and industry experts, they have gained a competitive edge and established themselves as industry leaders in precision engineering.Furthermore, this company's commitment to quality extends to their stringent quality control processes. Each part undergoes rigorous testing and inspection at every stage of the manufacturing process to ensure adherence to the highest standards. Their state-of-the-art inspection equipment enables them to measure and verify complex geometries and tolerances, guaranteeing the utmost precision and accuracy in every product.It is not just their cutting-edge technology and commitment to quality that sets this company apart; their dedication to customer satisfaction is equally remarkable. They work closely with their clients, understanding their unique requirements and providing tailored solutions to meet their needs. Their team of highly skilled engineers and technicians ensures efficient project management, from initial design to final production.The impact of this company's deep hole blind hole machining technology is significant, as it revolutionizes the production of intricate parts across a range of industries. The automotive sector, for example, benefits greatly from the ability to manufacture complex engine components with precision-engineered internal structures. The aerospace industry benefits from the production of lightweight yet strong components that enhance aircraft performance. The medical industry benefits from the development of intricate surgical instruments that improve patient outcomes. In essence, this company's technology enables advancements in various sectors crucial for societal development.In conclusion, deep hole blind hole machining has been revolutionized by this innovative company through their cutting-edge machinery, commitment to quality, and dedication to customer satisfaction. Their advanced technology and expertise have set a new standard in precision engineering, enabling the production of complex parts with unparalleled precision, accuracy, and efficiency. As they continue to push the boundaries of machining technology, this company remains at the forefront of the industry, driving advancements and transforming the way intricate parts are manufactured.
Honing Machine: Compact and Efficient Solution for Precision Metal Finishing
Title: Advanced Small Honing Machine Enriches Precision Manufacturing CapabilitiesIntroduction:In an era where precision is paramount, the demand for advanced machinery to achieve high-quality manufacturing has soared. Recognizing this evolving market, an industry-leading company has introduced its revolutionary Small Honing Machine, which promises to elevate the efficiency and precision of honing operations. This cutting-edge equipment is expected to accelerate production processes while maintaining supreme accuracy, meeting the ever-increasing needs of the manufacturing sector.Unleashing the Potential of Small Honing:Designed to meet the requirements of diverse industries, the Small Honing Machine raises the bar for honing operations by incorporating innovative features and state-of-the-art technology. This machine signifies a monumental leap forward in precision machining, providing businesses with the tools needed to achieve unprecedented levels of accuracy.Precision in Production:The Small Honing Machine offers unparalleled control over honing operations, ensuring optimum accuracy during the manufacturing process. Equipped with an advanced precision control system, this machine allows for precise adjustments, reducing the chances of errors and subsequent rework. This leads to minimized material wastage and increased productivity, resulting in substantial cost savings for businesses.Versatility and Flexibility:The versatility of the Small Honing Machine allows it to accommodate a wide range of materials, including metals, plastics, and composites. This adaptability ensures that manufacturers from various industries can benefit from this cutting-edge equipment. Whether used for honing cylinders, gears, or other precision components, this machine guarantees consistent and reliable results, meeting stringent quality requirements across different applications.Efficiency for Enhanced Productivity:With its advanced automation, the Small Honing Machine streamlines manufacturing processes, significantly reducing production time. The integration of cutting-edge robotics and software enables seamless coordination, eliminating the need for manual interventions and reducing human error. By automating key honing operations, manufacturers can experience enhanced efficiency, allowing them to meet tight deadlines and increase overall production capacity.User-Friendly Interface:The Small Honing Machine incorporates a user-friendly interface, making it easily accessible to both trained operators and newcomers to the field. The intuitive design of the control panel enables operators to monitor and adjust various parameters with ease, ensuring optimized honing performance. This user-centric approach sets the machine apart, facilitating quick setup, operation, and maintenance, thereby reducing downtime and maximizing production output.Sustainability and Energy Efficiency:In addition to its exceptional performance, the Small Honing Machine is designed with environmental consciousness in mind. Its energy-efficient system minimizes power consumption without compromising on productivity or precision. By prioritizing sustainable practices, manufacturers can contribute to a greener future and reduce their carbon footprint, aligning their operations with global sustainability objectives.Competitive Advantage for Businesses:The introduction of the Small Honing Machine provides businesses with a competitive edge in an increasingly demanding manufacturing landscape. This cutting-edge equipment facilitates higher throughput, tighter tolerances, and improved part quality, positioning manufacturers as industry leaders. It empowers businesses to take on complex projects, meet customer-specific requirements, and create custom solutions, elevating their market position and fostering long-term growth.Market Outlook and Conclusion:As precision manufacturing continues to gain prominence across industries, the Small Honing Machine emerges as a game-changer, revolutionizing honing operations. With its advanced features, versatility, user-friendly interface, and focus on sustainability, this equipment caters to the evolving needs of manufacturers worldwide. By embracing this technological breakthrough, businesses can elevate their precision manufacturing capabilities, ensuring their competitiveness in an increasingly globalized marketplace.
Revolutionary Solutions for Deep Hole Drilling: Unleashing New Possibilities
Title: Innovating Deep Hole Drilling Solutions Spearheading Industrial AdvancementsIntroduction:In today's fast-paced world, industrial sectors heavily rely on cutting-edge technologies to drive their growth and remain competitive in the market. Deep hole drilling is a specialized field that plays a critical role in industries such as aerospace, automotive, and oil and gas. One company at the forefront of providing innovative deep hole drilling solutions is pioneering a new era of precision and efficiency. By continuously pushing the boundaries of technology, this industry leader is reshaping operations and revolutionizing the manufacturing processes for clients worldwide.In this article, we delve into the profound impact of this cutting-edge company and its contributions to various industries. By focusing on the core principles that drive their success, we aim to highlight their commitment to delivering high-quality deep hole drilling solutions that exceed industry standards.Consistent Pursuit of Excellence:With years of experience in the field, this company has established itself as a trusted and reliable partner for clients seeking top-notch deep hole drilling solutions. Their unwavering dedication to excellence is evident through their ongoing pursuit of pioneering technologies and continuous improvement of their offerings.Expanding Capabilities:This industry leader has consistently expanded its capabilities to cater to the evolving demands of modern industries. By investing in research and development, they have harnessed the power of emerging technologies to enhance their deep hole drilling solutions. These advancements have resulted in increased efficiency, reduced operational costs, and improved precision for their clients.Collaborative Partnerships:Recognizing the importance of collaboration, this company actively engages with clients, understanding their unique requirements, and building long-lasting partnerships. By establishing effective communication channels, they tailor their deep hole drilling solutions to cater to specific industries, ensuring optimized performance and customer satisfaction.Adherence to Stringent Quality Standards:As a testament to their unwavering commitment to quality, this company maintains strict adherence to industry standards and regulations. By employing a comprehensive quality control system at every stage of their deep hole drilling process, they guarantee the utmost precision and reliability in their products.Industry Impact:The deep hole drilling solutions offered by this company have enabled significant advancements in critical sectors. In aviation and aerospace, their precision drilling technologies have facilitated the development of lightweight and fuel-efficient aircraft components. The automotive industry has benefited from their drilling solutions through the production of complex engine parts and advanced transmission systems. Moreover, this company's expertise in deep hole drilling has assisted in oil and gas exploration, resulting in improved extraction methods and enhanced efficiency.Continuous Innovation:Driven by a culture of innovation, this company consistently explores new horizons to bring forth breakthrough technologies. By embracing state-of-the-art techniques like laser drilling and electrochemical machining, they are reshaping the boundaries of what is possible in deep hole drilling. Their nimble approach to innovation ensures that they remain at the forefront of the industry.Conclusion:As industries worldwide continue to seek advanced manufacturing methods, the importance of companies specializing in deep hole drilling solutions becomes increasingly crucial. This industry leader, driven by their commitment to excellence and continuous innovation, is revolutionizing the landscape of precision drilling. By pushing the boundaries of technology and providing tailored solutions to various sectors, this company is instrumental in redefining industry standards and propelling global advancements.With a steadfast focus on quality, collaborative partnerships, and cutting-edge technologies, this company is poised to shape the future of deep hole drilling. As we witness the transformative power of their capabilities, it is clear that their dedication to delivering high-quality solutions will continue to propel industries toward greater heights of success.
Honing Machine Horizontal: A Definitive Guide to Achieving Precision Machining
Title: Innovations in Horizontal Honing Machines Revolutionize Manufacturing ProcessesIntroduction: In today's rapidly evolving manufacturing landscape, companies are constantly seeking cutting-edge technologies and equipment to enhance their productivity and output. Horizontal Honing Machines (HHD) have emerged as an integral tool in the precision machining industry, allowing manufacturers to achieve unparalleled precision and accuracy in their machining processes. In this article, we will explore the advancements made by an industry-leading company (name withheld) in the field of horizontal honing machines, and how these technologies are poised to revolutionize the manufacturing sector.Note: For the purpose of this article, the company name will be anonymized as "Company X".1. Evolution of Horizontal Honing Machines:Horizontal honing machines have evolved significantly over the years, transforming from conventional manual tools to highly sophisticated and automated systems. Company X has played a pivotal role in this evolution, introducing state-of-the-art technologies that have paved the way for enhanced efficiency and precision.2. Advanced Features and Functionality:One of the standout features of Company X's horizontal honing machines is their unparalleled automation capabilities. These machines incorporate cutting-edge systems that optimize the honing process, promoting significant time and cost savings. The integration of advanced controls, including computer numerical control (CNC), allows for precise control of honing parameters such as tool speed, stroke length, and feed rate, ensuring consistent and accurate results.3. Enhanced Precision and Accuracy:Company X has pioneered advancements in honing machine design, resulting in superior precision and accuracy compared to traditional honing methods. By incorporating sophisticated measuring systems and feedback mechanisms, these machines can precisely adjust the honing tool's position in real-time, eliminating errors and imperfections. This level of precision enables manufacturers to achieve tight tolerances and produce parts with exceptional surface finish.4. Versatility and Adaptability:Company X's horizontal honing machines are designed to accommodate a wide range of workpiece sizes and materials, making them suitable for diverse machining applications. Whether it's the honing of cylindrical, tubular, or contoured workpieces, these machines offer flexibility and adaptability, reducing setup times and optimizing production cycles. Moreover, the customizable tooling options allow manufacturers to address various honing requirements to achieve optimal results.5. Improved Efficiency and Productivity:The introduction of X's innovative horizontal honing machines has resulted in significant improvements in production efficiency. The automated nature of these machines, combined with their ability to integrated robotic loading and unloading systems, minimizes human intervention and streamlines the overall manufacturing process. This results in increased throughput, reduced cycle times, and improved overall productivity.6. Intelligent Monitoring and Maintenance:Company X's horizontal honing machines utilize intelligent monitoring systems that continuously track crucial operating parameters. Real-time data analysis allows the detection of anomalies, potential issues, or performance deviations, facilitating proactive maintenance and minimizing unplanned downtime. This predictive maintenance approach ensures maximum machine uptime and prolongs the longevity of the equipment.Conclusion:The advancements made by Company X in horizontal honing machines have significantly enhanced the manufacturing processes across diverse industries. With their unmatched precision, automation capabilities, and versatility, these machines have become invaluable assets for manufacturers seeking to optimize productivity, improve quality, and achieve cost-effectiveness. As manufacturers continue to embrace advanced technologies, horizontal honing machines are expected to play a crucial role in driving innovation and shaping the future of the precision machining industry.
Enhance Your Manufacturing Process with Advanced CNC Deep Hole Drilling Techniques
Title: Revolutionary CNC Deep Hole Drilling Technology Sets New Standards in ManufacturingIntroduction:In today's highly competitive manufacturing industry, precision and efficiency hold the key to success. As a pioneer in the field, company {} has unveiled its cutting-edge CNC Deep Hole Drilling technology, which promises to revolutionize the way parts and components are manufactured. By integrating the latest advancements in machining and automation, this groundbreaking solution aims to significantly improve productivity and quality while reducing production costs.1. Challenges in Traditional Deep Hole Drilling Techniques:Traditionally, deep hole drilling has been a labor-intensive and time-consuming process, requiring specialized equipment and skilled operators. Moreover, achieving high levels of precision and surface finish has been a daunting task. These challenges have limited the scalability and efficiency of deep hole drilling, hindering further advancements in the manufacturing industry.2. The Evolution of CNC Deep Hole Drilling:Recognizing the need for a more efficient and precise solution, {} developed the CNC Deep Hole Drilling technology. By leveraging computer numerical control (CNC) systems, this technology streamlines the entire drilling process, enabling faster production cycles and unparalleled accuracy. Whether it's for aerospace, automotive, medical, or mold and die industries, this innovation offers significant benefits to manufacturers globally.3. Unprecedented Precision and Quality:The CNC Deep Hole Drilling technology utilizes advanced sensors and monitoring systems, ensuring the precise measurement of drilling depth, diameter, and surface finish. This level of control enables manufacturers to achieve the tightest tolerances, resulting in parts and components with superior quality. By reducing human error and enhancing repeatability, this technology greatly minimizes the risk of defects, waste, and rework.4. Enhanced Efficiency and Productivity:With its automated features, the CNC Deep Hole Drilling technology optimizes the manufacturing process, eliminating the need for time-consuming manual interventions. The integration of intelligent chip management systems prevents chip accumulation, enhancing drilling efficiency and prolonging tool life. Moreover, the system's ability to perform multiple drilling operations simultaneously reduces cycle times, boosting overall productivity.5. Cost Reduction and Resource Optimization:By maximizing efficiency and minimizing material waste, the CNC Deep Hole Drilling technology leads to significant cost savings for manufacturers. The precise measurement and control of drilling parameters minimize the consumption of feedstock, reducing material costs. Additionally, the integrated coolant systems ensure efficient heat dissipation, preventing tool wear and extending tool life, thereby reducing the need for frequent tool replacements.6. Versatility and Adaptability:One of the key advantages of the CNC Deep Hole Drilling technology is its versatility. The system can handle a wide range of materials, including steels, alloys, composites, and non-metals, adapting to diverse manufacturing requirements. This flexibility allows manufacturers to explore new product designs and expand their offerings, catering to a variety of industries and applications.7. Future Prospects and Market Impact:The introduction of the CNC Deep Hole Drilling technology by {} is expected to have a profound impact on the manufacturing industry. With its advanced capabilities, this solution promises to spur innovation and drive progress in various sectors. The improved precision, efficiency, and cost-effectiveness offered by this technology will enable manufacturers to meet increasing market demands while maintaining a competitive edge.Conclusion:As manufacturing continues to advance, the demand for faster, more accurate, and cost-effective production techniques grows. The CNC Deep Hole Drilling technology introduced by {} sets new standards in precision machining and automation. Its ability to deliver unprecedented precision, enhance efficiency, and reduce costs ensures its crucial role in shaping the future of manufacturing. With this innovative solution, manufacturers can look forward to improved productivity, higher quality parts, and a sustainable competitive advantage.