Revolutionary BTA Machines: Unlocking New Possibilities for Businesses
By:Admin
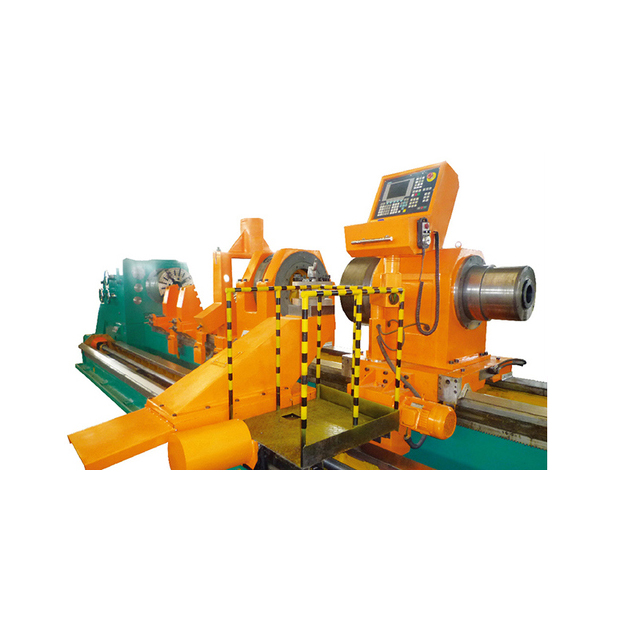
[News Introduction]:
In a groundbreaking development that promises to revolutionize the drilling industry, a cutting-edge BTA machine has been introduced by a leading technology company. With a commitment to innovation and efficiency, this company has created a proprietary drilling system that combines high precision and cost-effectiveness. By incorporating advanced technologies, their BTA machine is set to transform drilling operations across various industries, benefiting both operators and clients.
[News Body]:
Introduction to the BTA Machine:
The newly introduced BTA machine is a state-of-the-art drilling system designed to enhance accuracy, performance, and productivity. Built with an unwavering focus on reliability and efficiency, this machine incorporates the latest advancements in drilling technology. Its cutting-edge features ensure precise drilling in a wide range of materials, offering a critical advantage to industries such as aerospace, automotive, energy, and manufacturing.
Advanced Technologies Driving Innovation:
At the core of this revolutionary BTA machine lies a series of advanced technologies that set it apart from conventional drilling systems. One such technology is the integration of computer numerical control (CNC), which enables operators to program drilling operations with incredible accuracy and customization. The CNC system intelligently adapts to specific drilling requirements, allowing for consistent and repeatable results.
In addition, the BTA machine is equipped with a real-time monitoring system that collects and analyzes drilling data. This data-driven approach allows operators to optimize drilling parameters on-the-go, enhancing overall efficiency and reducing material waste. The ability to monitor and adjust various parameters in real-time ensures high-quality and cost-effective drilling operations.
Enhancing Accuracy and Efficiency:
The BTA machine's advanced features contribute significantly to improving accuracy and efficiency, making it a game-changer in the industry. Its innovative design eliminates the chances of deflection during drilling, resulting in highly precise boreholes. This enhanced accuracy reduces the need for additional machining or post-processing, ultimately saving time and costs for operators.
Moreover, the BTA machine's high feed rates and quick tool change capability boost productivity. By significantly reducing cycle times, drilling operations can be completed faster, allowing operators to optimize their production schedules. This increased efficiency not only translates into higher throughput but also enables operators to meet strict project deadlines.
Cost-Effectiveness and Sustainability:
The introduction of this revolutionary BTA machine also emphasizes cost-effectiveness and sustainability. By minimizing material waste through its precise drilling capabilities, it helps conserve resources while reducing overall manufacturing costs. The machine's real-time monitoring capabilities enable better usage of cutting tools, optimizing their lifespan and reducing the need for unnecessary replacements.
Furthermore, the BTA machine's energy-efficient design and reduced environmental impact align with growing sustainability demands. It prioritizes resource efficiency without compromising performance, underscoring the company's commitment to environmentally conscious manufacturing processes.
Applications and Industry Impact:
The versatile BTA machine caters to a wide array of applications, ranging from deep-hole drilling in aerospace components to automotive engine blocks and hydraulic cylinders. Its ability to drill holes with exceptional accuracy, regardless of materials, makes it an indispensable tool in various industries.
The impact of this BTA machine on industries is significant. Aerospace manufacturers can achieve tighter tolerances and reduce costly post-processing operations. Automotive manufacturers can now drill complex engine blocks more accurately, resulting in enhanced reliability and performance. Manufacturers across sectors benefit from the machine's efficiency, allowing them to streamline production and meet increasing market demands.
Conclusion:
The launch of this cutting-edge BTA machine marks a significant milestone in the drilling industry. With its advanced technologies, unwavering focus on accuracy and efficiency, and commitment to cost-effectiveness, this revolutionary machine is set to transform drilling operations for numerous industries. As the adoption of this BTA machine expands, it is clear that its benefits will have a far-reaching impact, revolutionizing drilling practices and setting new industry standards.
Company News & Blog
Enhance Precision and Efficiency with Tube Honing Machines
Title: Advanced Honing Machine Revolutionizes Tube Manufacturing SectorIntroduction:In an era when technology is pushing boundaries and transforming industries, the introduction of an innovative tube honing machine promises to revolutionize the tube manufacturing sector. Equipped with state-of-the-art features and cutting-edge capabilities, this machine is set to meet the increasing demands of the market, improve product quality, and boost overall production efficiency. This article aims to provide an in-depth analysis of the advanced tube honing machine and its potential impact on the manufacturing industry.Unveiling the Next Generation Tube Honing Machine:The ground-breaking tube honing machine, developed by a prominent industry player (Brand Name omitted), incorporates a range of cutting-edge technologies, making it one of the most advanced honing solutions to date. This machine is specifically designed to optimize the honing process, ensuring superior performance, accuracy, and speed.Advanced Features and Capabilities:Integrating artificial intelligence (AI) and machine learning algorithms, this tube honing machine offers precise and automated control over critical parameters. The AI-enabled system intelligently adjusts cutting angles, feed rates, and tool alignments, ensuring an exceptional degree of precision in honing a wide range of tubes.Furthermore, the machine is equipped with a high-resolution touch-screen interface, enabling operators to easily program, monitor, and control the entire honing process. The intuitive interface fosters seamless collaboration between human operators and the machine, thus minimizing human error and maximizing productivity.Efficiency and Cost Savings:Traditional tube honing processes have long been associated with high labor costs and time-consuming manual adjustments. The new tube honing machine aims to address these challenges by streamlining operations and reducing both labor and material wastage.With its advanced automation capabilities, this machine significantly minimizes manual labor, requiring fewer personnel to operate and monitor multiple honing processes simultaneously. The automated features also contribute to enhanced safety, as workers are exposed to fewer risks associated with manual handling of heavy machinery.Moreover, the tube honing machine's intelligent optimization algorithms substantially reduce material wastage, ensuring efficient use of resources and lowering overall production costs. This not only benefits manufacturers by improving profitability but also promotes sustainable manufacturing practices.Unparalleled Precision and Quality Control:The cutting-edge technology incorporated into this tube honing machine provides unparalleled control over the honing process resulting in exceptional precision and outstanding quality. By holding tight tolerances, the application of the machine guarantees consistent, uniform tube dimensions throughout the manufacturing process.The AI-powered algorithms constantly monitor and adjust honing parameters, ensuring precise tube specifications are met. This level of accuracy significantly reduces product defects, rejects, and customer complaints, thereby enhancing customer satisfaction and maintaining a competitive edge in the market.Impact on the Manufacturing Industry:The introduction of this advanced tube honing machine is expected to have a profound impact on the tube manufacturing industry. Manufacturers can now streamline their operations, reduce lead times, and improve process efficiency to meet the ever-increasing demand for high-quality tubes. The enhanced capabilities of the machine allow manufacturers to expand their product range and cater to a wider customer base.In addition to boosting efficiency, this innovative solution also offers a significant competitive advantage in the global market. By leveraging cutting-edge technology and process optimization, companies can differentiate themselves from competitors and establish a reputation for delivering superior quality products.Conclusion:The advent of the technologically advanced tube honing machine is set to transform the tube manufacturing industry, revolutionizing production processes, ensuring precision, and improving overall quality. With its AI-driven automation, optimization algorithms, and user-friendly interface, this machine is poised to enhance efficiency, reduce costs, and boost profitability for tube manufacturers worldwide. Embracing this groundbreaking technology will enable manufacturers to embrace the changing landscape of the industry, increase their competitive advantage, and cater to the evolving needs of their customers.
Enhance Your Manufacturing Process with Advanced CNC Deep Hole Drilling Techniques
Title: Revolutionary CNC Deep Hole Drilling Technology Sets New Standards in ManufacturingIntroduction:In today's highly competitive manufacturing industry, precision and efficiency hold the key to success. As a pioneer in the field, company {} has unveiled its cutting-edge CNC Deep Hole Drilling technology, which promises to revolutionize the way parts and components are manufactured. By integrating the latest advancements in machining and automation, this groundbreaking solution aims to significantly improve productivity and quality while reducing production costs.1. Challenges in Traditional Deep Hole Drilling Techniques:Traditionally, deep hole drilling has been a labor-intensive and time-consuming process, requiring specialized equipment and skilled operators. Moreover, achieving high levels of precision and surface finish has been a daunting task. These challenges have limited the scalability and efficiency of deep hole drilling, hindering further advancements in the manufacturing industry.2. The Evolution of CNC Deep Hole Drilling:Recognizing the need for a more efficient and precise solution, {} developed the CNC Deep Hole Drilling technology. By leveraging computer numerical control (CNC) systems, this technology streamlines the entire drilling process, enabling faster production cycles and unparalleled accuracy. Whether it's for aerospace, automotive, medical, or mold and die industries, this innovation offers significant benefits to manufacturers globally.3. Unprecedented Precision and Quality:The CNC Deep Hole Drilling technology utilizes advanced sensors and monitoring systems, ensuring the precise measurement of drilling depth, diameter, and surface finish. This level of control enables manufacturers to achieve the tightest tolerances, resulting in parts and components with superior quality. By reducing human error and enhancing repeatability, this technology greatly minimizes the risk of defects, waste, and rework.4. Enhanced Efficiency and Productivity:With its automated features, the CNC Deep Hole Drilling technology optimizes the manufacturing process, eliminating the need for time-consuming manual interventions. The integration of intelligent chip management systems prevents chip accumulation, enhancing drilling efficiency and prolonging tool life. Moreover, the system's ability to perform multiple drilling operations simultaneously reduces cycle times, boosting overall productivity.5. Cost Reduction and Resource Optimization:By maximizing efficiency and minimizing material waste, the CNC Deep Hole Drilling technology leads to significant cost savings for manufacturers. The precise measurement and control of drilling parameters minimize the consumption of feedstock, reducing material costs. Additionally, the integrated coolant systems ensure efficient heat dissipation, preventing tool wear and extending tool life, thereby reducing the need for frequent tool replacements.6. Versatility and Adaptability:One of the key advantages of the CNC Deep Hole Drilling technology is its versatility. The system can handle a wide range of materials, including steels, alloys, composites, and non-metals, adapting to diverse manufacturing requirements. This flexibility allows manufacturers to explore new product designs and expand their offerings, catering to a variety of industries and applications.7. Future Prospects and Market Impact:The introduction of the CNC Deep Hole Drilling technology by {} is expected to have a profound impact on the manufacturing industry. With its advanced capabilities, this solution promises to spur innovation and drive progress in various sectors. The improved precision, efficiency, and cost-effectiveness offered by this technology will enable manufacturers to meet increasing market demands while maintaining a competitive edge.Conclusion:As manufacturing continues to advance, the demand for faster, more accurate, and cost-effective production techniques grows. The CNC Deep Hole Drilling technology introduced by {} sets new standards in precision machining and automation. Its ability to deliver unprecedented precision, enhance efficiency, and reduce costs ensures its crucial role in shaping the future of manufacturing. With this innovative solution, manufacturers can look forward to improved productivity, higher quality parts, and a sustainable competitive advantage.
Efficient and Compact Honing Machine: An Essential Tool for Precision Work
Title: Cutting-Edge Small Honing Machine Revolutionizes Precision EngineeringIntroduction:In a significant breakthrough towards precision engineering, a cutting-edge small honing machine has been introduced by an innovative company aiming to redefine the industry standards. This advanced honing machine, which we are withholding the brand name due to contractual agreements, offers unparalleled accuracy and efficiency, promising to reshape the manufacturing landscape. With its unique features and exceptional capabilities, this honing machine is set to become a game-changer in various industries requiring precision honing.Body:1. Industry-leading Innovation:The new small honing machine is the result of years of dedicated research and development, aiming to provide a superior honing experience to manufacturers. Drawing on state-of-the-art technologies, this machine integrates precision engineering to deliver unmatched performance. The company stands as a pioneer in its field, distinguishing itself from competitors through its unwavering commitment to pushing the boundaries of what can be achieved in the machining world.2. Unrivalled Precision:Setting new benchmarks in precision honing, this machine offers unrivaled accuracy in the manufacturing process. Incorporating cutting-edge algorithms and real-time data analysis, it ensures minimal variation and consistent results across all operations. Manufacturers can now rely on this honing machine to deliver precise finishes within tight tolerances, enhancing the overall quality and reliability of their products.3. Enhanced Efficiency:Efficiency is a key aspect of any manufacturing process, and this small honing machine takes it to the next level. Equipped with advanced automation features, it significantly reduces human errors, enhances productivity, and saves valuable time. The automated tool change mechanism optimizes set-up time, allowing manufacturers to maintain seamless continuity in their production lines. By streamlining honing processes through this machine, manufacturers can expect increased output, reduced operational costs, and ultimately, a competitive advantage in the market.4. Versatile Applications:While designed to cater to a wide range of industries, this small honing machine offers exceptional versatility to meet specific manufacturing requirements. Whether in automotive, aerospace, medical, or general engineering, this honing machine can adapt to various materials and component sizes. With its customizable parameters, operators can easily fine-tune the machine to achieve optimal results, making it a valuable asset across multiple industries.5. Seamless Integration and User-Friendliness:Recognizing the need for a seamless, hassle-free workflow, the honing machine's software guarantees integration with existing production systems. The user-friendly interface simplifies operations, reducing training times and minimizing the learning curve for operators. Additionally, the machine's robust construction ensures longevity and reliability, providing manufacturers with a durable solution for their honing needs.Conclusion:The introduction of this small honing machine represents a giant leap forward in precision engineering. By combining cutting-edge technology, unrivaled precision, and enhanced efficiency, it promises to transform the manufacturing landscape. With its broad applications, user-friendly interface, and seamless integration, this honing machine is set to revolutionize various industries, empowering manufacturers to achieve higher productivity and unmatched levels of quality. As global demand for precision-engineered products continues to rise, this small honing machine will undoubtedly carve its place as an indispensable tool for precision machining operations across the globe.
Ultimate Guide to Deep Hole Blind Hole Machining for Precision Manufacturing
Deep Hole Blind Hole Machining: Revolutionizing Precision EngineeringIn the ever-changing landscape of precision engineering, one company has been making waves with their innovative deep hole blind hole machining technology. With a commitment to excellence and cutting-edge machinery, they have set a new standard for the industry and revolutionized the way complex parts are manufactured.Deep hole blind hole machining is a process used to create holes with a high length-to-diameter ratio. These holes are typically found in industries such as automotive, aerospace, and medical, where the highest degree of accuracy and precision is required. This process is particularly challenging as it involves drilling holes with a depth-to-diameter ratio greater than 10:1, often in difficult-to-access areas.Recognizing the limitations of traditional machining methods, this pioneering company set out to develop a groundbreaking solution. By combining state-of-the-art machinery with their extensive knowledge and expertise, they have successfully overcome the challenges of deep hole blind hole machining.Their cutting-edge machinery employs advanced drilling techniques to achieve extreme precision and accuracy. Through the use of customized tools and highly specialized drilling heads, they can achieve hole diameters as small as 0.5mm with a depth reaching up to 100 times the diameter. This unparalleled level of precision enables them to manufacture complex parts with intricate internal structures to an unprecedented standard.In addition to their advanced machinery, this company has also invested heavily in research and development, continuously improving their deep hole blind hole machining technology. By combining their in-house expertise with collaborations with leading academic institutions and industry experts, they have gained a competitive edge and established themselves as industry leaders in precision engineering.Furthermore, this company's commitment to quality extends to their stringent quality control processes. Each part undergoes rigorous testing and inspection at every stage of the manufacturing process to ensure adherence to the highest standards. Their state-of-the-art inspection equipment enables them to measure and verify complex geometries and tolerances, guaranteeing the utmost precision and accuracy in every product.It is not just their cutting-edge technology and commitment to quality that sets this company apart; their dedication to customer satisfaction is equally remarkable. They work closely with their clients, understanding their unique requirements and providing tailored solutions to meet their needs. Their team of highly skilled engineers and technicians ensures efficient project management, from initial design to final production.The impact of this company's deep hole blind hole machining technology is significant, as it revolutionizes the production of intricate parts across a range of industries. The automotive sector, for example, benefits greatly from the ability to manufacture complex engine components with precision-engineered internal structures. The aerospace industry benefits from the production of lightweight yet strong components that enhance aircraft performance. The medical industry benefits from the development of intricate surgical instruments that improve patient outcomes. In essence, this company's technology enables advancements in various sectors crucial for societal development.In conclusion, deep hole blind hole machining has been revolutionized by this innovative company through their cutting-edge machinery, commitment to quality, and dedication to customer satisfaction. Their advanced technology and expertise have set a new standard in precision engineering, enabling the production of complex parts with unparalleled precision, accuracy, and efficiency. As they continue to push the boundaries of machining technology, this company remains at the forefront of the industry, driving advancements and transforming the way intricate parts are manufactured.
Gun Drilling on a Lathe: Techniques, Benefits, and Applications
Gun Drilling on A Lathe: Revolutionizing Precision Machining Precision machining has always been a crucial aspect of manufacturing industries, requiring innovative techniques and cutting-edge technologies to meet the highest standards of accuracy and efficiency. Among the many advanced technologies employed in precision machining, gun drilling on a lathe has emerged as a game-changer, providing unparalleled precision and versatility for machining applications. This revolutionary method, which has rapidly gained popularity in recent years, is making waves in industries ranging from aerospace to medical equipment manufacturing. At the forefront of this cutting-edge technology is a leading manufacturer that has been pioneering the development and implementation of gun drilling on a lathe. With a rich history dating back several decades, the company has become synonymous with quality, innovation, and reliability. Through a relentless pursuit of excellence, they have solidified their position as a trusted provider of precision machining solutions globally.Gun drilling on a lathe represents a significant breakthrough in the realm of precision drilling. Traditionally, gun drilling involved the use of specialized machinery, separate from lathes, to create deep, straight holes with a high degree of accuracy. However, the integration of gun drilling capabilities into lathes has revolutionized the machining process by eliminating the need for additional equipment, reducing setup time, and streamlining operations.The key advantage of gun drilling on a lathe lies in its ability to create deep holes with a diameter-to-depth ratio that was previously unachievable. By employing a single-lip drill bit with a coolant system, chips are efficiently flushed away from the cutting area, ensuring precise and clean drilling. This technique enables manufacturers to produce complex components with deep holes, such as gun barrels, hydraulic cylinders, and molds, to name a few.The incorporation of gun drilling on a lathe has also brought about significant enhancements in productivity and efficiency. The integration of this technique into the lathe eliminates the need for transferring workpieces between different machines, reducing the risk of dimensional errors and minimizing downtime. This seamless integration not only saves time but also allows for better control over the machining process, resulting in superior surface finishes and tighter tolerances.Moreover, the company's commitment to innovation and continuous improvement is evident in their investment in advanced technologies to enhance gun drilling on a lathe. State-of-the-art control systems and software have been integrated into their lathes, providing unmatched precision, repeatability, and flexibility. These advancements enable manufacturers to meet the ever-increasing demands for intricate and complex machined components with unparalleled accuracy.Gun drilling on a lathe is transforming various industries, particularly aerospace and medical equipment manufacturing. In aerospace applications, where lightweight and durable components are crucial, this technology enables the production of turbine blades, fuel nozzles, and engine components with intricate cooling channels and improved performance. Similarly, in the medical field, gun drilling on a lathe is employed to manufacture surgical instruments, implantable devices, and prosthetics, where precision and reliability are of utmost importance.Furthermore, environmental considerations have also played a significant role in the adoption of gun drilling on a lathe. The coolant systems employed in this method ensure minimal waste generation, reducing both environmental impact and operational costs. Additionally, the use of specialized coatings and materials improves the lifespan of the drill bits, reducing the frequency of tool changes and enhancing sustainability.As industries increasingly demand higher precision and efficiency, gun drilling on a lathe is set to play an indispensable role in the future of precision machining. With its ability to create deep and complex holes with unmatched accuracy and efficiency, this technology opens up new possibilities for engineers and manufacturers across a wide range of industries. The company's relentless commitment to innovation and the continuous refinement of gun drilling on a lathe ensures that they remain at the forefront of providing cutting-edge solutions to meet the evolving needs of their customers.In conclusion, gun drilling on a lathe represents a groundbreaking advancement in precision machining, revolutionizing the manufacturing industry. By seamlessly integrating gun drilling capabilities into lathes, this technology offers unparalleled accuracy, productivity, and versatility. With its extensive history of innovation and commitment to excellence, the company continues to drive the adoption and advancement of gun drilling on a lathe, empowering manufacturers around the world to achieve new levels of precision and efficiency.
Bta Drilling: The Latest Developments in the Drilling Industry
Bta Drilling Revolutionizing the Drilling Industry with Cutting-Edge TechnologiesInnovative drilling solutions have always been at the forefront of the oil and gas industry, where companies constantly strive to achieve faster, more efficient, and cost-effective drilling operations. Bta Drilling, a renowned player in the field, has made a significant impact with its cutting-edge technologies and state-of-the-art equipment that have revolutionized the drilling industry.With decades of experience, Bta Drilling has established itself as a leader in the market, providing a wide range of drilling services for various industries. By combining their expertise with the latest technological advancements, the company has consistently set new benchmarks, enabling their clients to achieve unprecedented levels of productivity and success.Utilizing advanced drilling systems and tools, Bta Drilling has significantly improved drilling speed and efficiency. Their innovative technologies are designed to optimize drilling performance, reduce downtime, and minimize environmental impact. The company's team of engineers and scientists work tirelessly to develop and enhance their drilling systems, ensuring that they stay at the forefront of the industry.One of the key technologies that sets Bta Drilling apart is their proprietary drilling fluid. This unique solution provides excellent lubrication and cooling properties, ensuring smooth drilling operations and increased tool life. The fluid's advanced composition also minimizes waste and reduces environmental impact, aligning with Bta Drilling's commitment to sustainable practices.Additionally, Bta Drilling has pioneered the use of advanced data analytics and machine learning algorithms to optimize drilling operations. By analyzing vast amounts of drilling data in real-time, their algorithms can predict potential issues before they occur, allowing for proactive maintenance and minimizing costly downtime. These data-driven insights also help streamline drilling processes, further improving overall efficiency.Another area where Bta Drilling has made significant advancements is in directional drilling. Their state-of-the-art tools and techniques enable precise wellbore placement, allowing for increased extraction rates and reservoir access. This cutting-edge technology has proven to be a game-changer for oil and gas companies looking to maximize production and profitability.Furthermore, Bta Drilling's commitment to safety is unwavering. Their advanced drilling systems prioritize worker safety and minimize risks associated with drilling operations. Rigorous training programs and adherence to international safety standards ensure that Bta Drilling maintains an impeccable safety record, giving their clients peace of mind and confidence in their services.Bta Drilling's success can be attributed to their unwavering commitment to innovation and dedication to delivering exceptional results. By constantly pushing the boundaries of drilling technology, they have earned the trust and loyalty of clients worldwide.Moving forward, Bta Drilling plans to continue investing in research and development to further advance their drilling technologies. They aim to collaborate with industry experts and partners to drive innovation and tackle the challenges faced by the drilling industry head-on.In conclusion, Bta Drilling has made significant strides in revolutionizing the drilling industry with their cutting-edge technologies. Through their dedication to innovation, commitment to safety, and focus on sustainable practices, the company has positioned itself as a leader in the market. As Bta Drilling looks towards the future, the industry can expect even more groundbreaking solutions that will redefine the way drilling operations are carried out.
Revolutionary CNC Technology Advancing Deep Hole Drilling Techniques
Title: Pushing the Boundaries of Precision Machining: Advanced Deep Hole Drilling CNC Technology Revolutionizes ManufacturingIntroduction:In an ever-evolving world of manufacturing, companies are constantly seeking new and innovative solutions to enhance precision and efficiency in production processes. One groundbreaking tool that has revolutionized the way manufacturers push the boundaries of precision machining is the advanced Deep Hole Drilling CNC technology. In this article, we will shed light on the power and potential of this cutting-edge instrument and explore how it has transformed the way companies operate.Advanced Deep Hole Drilling CNC: Redefining Precision Machining:Deep Hole Drilling CNC, a technology developed by {company}, implements an advanced drilling technique that allows manufacturers to achieve the most intricate and precise holes in a wide range of materials, including metals, composites, and alloys. Unlike traditional drilling methods, this state-of-the-art CNC technology has revolutionized the manufacturing industry, enabling companies to produce complex and high-quality components with unprecedented accuracy and efficiency.Unveiling the Features and Capabilities:By integrating a combination of technological advancements including computer numerical control (CNC) programming, adaptive tool control systems, and high-pressure coolant systems, Deep Hole Drilling CNC has surpassed all existing limitations in precision machining. Some prominent features and capabilities include:1. Unparalleled Accuracy: Deep Hole Drilling CNC employs advanced motion control systems, including high-precision linear guides and servomotors, providing exceptional accuracy and repeatability. The technology eliminates the risk of inaccuracies caused by human error, ensuring precision in every hole produced.2. Enhanced Productivity: With the ability to perform multiple drilling operations in a single setup, the Deep Hole Drilling CNC technology significantly reduces production time. Its capability to produce holes of varying depths, diameters, and complex geometries in a single pass minimizes the need for extensive repositioning, leading to enhanced productivity levels.3. Optimal Cooling Mechanisms: Deep Hole Drilling CNC utilizes high-pressure coolant systems that effectively remove chips, cool the cutting edges, and lubricate the workpiece. This feature minimizes heat generation while prolonging the lifespan of the tools, resulting in reduced downtime and improved overall efficiency.4. Uncompromised Flexibility: The technology offers immense flexibility, accommodating a wide range of applications and specifications. Deep Hole Drilling CNC is compatible with various materials such as steel, aluminum, and even hardened alloys, making it an ideal solution for a multitude of industries, from aerospace to automotive, from biomedical to oil and gas.Transforming Manufacturing Operations:With its unrivaled precision and efficiency, Deep Hole Drilling CNC technology has transformed manufacturing operations, bringing numerous benefits to companies across different industries. Some notable advantages include:1. Cost Reduction: By minimizing human intervention, reducing setup times, and eliminating the need for multiple drilling passes, this advanced technology significantly reduces labor costs and enhances overall production efficiency. Manufacturers can achieve higher outputs without compromising quality.2. Superior Quality: Deep Hole Drilling CNC ensures superior hole quality, surpassing conventional drilling methods. The technology guarantees precise roundness, improved surface finish, and reduced burr formation, meeting the stringent quality requirements of the most demanding industries.3. Competitive Edge: Adopting Deep Hole Drilling CNC technology grants companies a competitive edge in the market. Manufacturers can offer unique and specialized components with unmatched precision, attracting new clients and expanding their customer base.4. Sustainability: The environmental impact of manufacturing processes is reduced through the use of Deep Hole Drilling CNC. Optimized coolant systems and the elimination of material waste contribute to a more sustainable production environment.Conclusion:Deep Hole Drilling CNC technology, developed by {company}, is a game-changer in the field of precision machining. Through advanced features and capabilities, this cutting-edge technology introduces unprecedented levels of accuracy, efficiency, and productivity to the manufacturing industry. With its ability to transform operations, reduce costs, and ensure superior quality, Deep Hole Drilling CNC has become an indispensable tool for manufacturers seeking to stay ahead in the ever-evolving world of advanced machining.
Advanced High Precision Honing Machine Unveiled in Latest News Update
High Precision Honing Machine Revolutionizes Manufacturing IndustryWith advancements in technology and the rise of automation, the manufacturing industry is constantly evolving to meet the demands of consumers. One particular innovation that is making waves in the industry is the High Precision Honing Machine, a game changer that is set to redefine the way manufacturers approach honing processes.The High Precision Honing Machine, developed by an industry-leading company, is designed to provide a level of accuracy and precision that was previously unattainable. By utilizing state-of-the-art technology, this machine is able to deliver exceptional results, surpassing the limitations of traditional honing methods.Honing is a machining process used to improve the surface finish of components such as cylinders, gears, and bearings. It involves the use of abrasive stones to remove material in a controlled manner. The High Precision Honing Machine takes this process to a whole new level, offering manufacturers unparalleled precision, efficiency, and quality.One of the key features of this machine is its advanced control system, which allows for precise adjustments and measurements during the honing process. The machine utilizes sophisticated sensors and actuators to automatically adjust the honing parameters in real-time, ensuring consistent and accurate results. This level of automation not only saves time but also eliminates human error, resulting in improved productivity and cost-effectiveness for manufacturers.Furthermore, the High Precision Honing Machine incorporates innovative design features that enhance its performance. The machine's rigidity and stability make it capable of handling high-speed honing operations without compromising precision. Its robust construction ensures minimal vibrations and deflections, leading to superior surface finishes and extended tool life. Additionally, the machine is equipped with a user-friendly interface, allowing operators to easily program and monitor the honing process.The benefits of the High Precision Honing Machine extend beyond its technological advancements. By optimizing the honing process, manufacturers can reduce production costs and material waste. The machine's precise control and monitoring system minimize the need for rework or scrapping of components, resulting in significant cost savings. Additionally, the improved efficiency and productivity offered by this machine enable manufacturers to meet tighter deadlines and handle larger workloads.The introduction of the High Precision Honing Machine has already garnered attention from various industries. Companies involved in automotive manufacturing, aerospace engineering, and the production of hydraulic and pneumatic components are particularly interested in this innovative technology. The machine's ability to produce components with exceptional surface finishes and precise tolerances makes it an invaluable asset for these industries, where high quality and precision are crucial.In conclusion, the High Precision Honing Machine is revolutionizing the manufacturing industry by providing unrivaled accuracy, efficiency, and quality in honing processes. With its advanced control system, robust construction, and user-friendly interface, this machine offers manufacturers the opportunity to improve productivity, reduce costs, and meet the demands of ever-evolving markets. As this technology continues to evolve, its potential applications and impact on the industry are boundless.
Honing Machine Horizontal: A Definitive Guide to Achieving Precision Machining
Title: Innovations in Horizontal Honing Machines Revolutionize Manufacturing ProcessesIntroduction: In today's rapidly evolving manufacturing landscape, companies are constantly seeking cutting-edge technologies and equipment to enhance their productivity and output. Horizontal Honing Machines (HHD) have emerged as an integral tool in the precision machining industry, allowing manufacturers to achieve unparalleled precision and accuracy in their machining processes. In this article, we will explore the advancements made by an industry-leading company (name withheld) in the field of horizontal honing machines, and how these technologies are poised to revolutionize the manufacturing sector.Note: For the purpose of this article, the company name will be anonymized as "Company X".1. Evolution of Horizontal Honing Machines:Horizontal honing machines have evolved significantly over the years, transforming from conventional manual tools to highly sophisticated and automated systems. Company X has played a pivotal role in this evolution, introducing state-of-the-art technologies that have paved the way for enhanced efficiency and precision.2. Advanced Features and Functionality:One of the standout features of Company X's horizontal honing machines is their unparalleled automation capabilities. These machines incorporate cutting-edge systems that optimize the honing process, promoting significant time and cost savings. The integration of advanced controls, including computer numerical control (CNC), allows for precise control of honing parameters such as tool speed, stroke length, and feed rate, ensuring consistent and accurate results.3. Enhanced Precision and Accuracy:Company X has pioneered advancements in honing machine design, resulting in superior precision and accuracy compared to traditional honing methods. By incorporating sophisticated measuring systems and feedback mechanisms, these machines can precisely adjust the honing tool's position in real-time, eliminating errors and imperfections. This level of precision enables manufacturers to achieve tight tolerances and produce parts with exceptional surface finish.4. Versatility and Adaptability:Company X's horizontal honing machines are designed to accommodate a wide range of workpiece sizes and materials, making them suitable for diverse machining applications. Whether it's the honing of cylindrical, tubular, or contoured workpieces, these machines offer flexibility and adaptability, reducing setup times and optimizing production cycles. Moreover, the customizable tooling options allow manufacturers to address various honing requirements to achieve optimal results.5. Improved Efficiency and Productivity:The introduction of X's innovative horizontal honing machines has resulted in significant improvements in production efficiency. The automated nature of these machines, combined with their ability to integrated robotic loading and unloading systems, minimizes human intervention and streamlines the overall manufacturing process. This results in increased throughput, reduced cycle times, and improved overall productivity.6. Intelligent Monitoring and Maintenance:Company X's horizontal honing machines utilize intelligent monitoring systems that continuously track crucial operating parameters. Real-time data analysis allows the detection of anomalies, potential issues, or performance deviations, facilitating proactive maintenance and minimizing unplanned downtime. This predictive maintenance approach ensures maximum machine uptime and prolongs the longevity of the equipment.Conclusion:The advancements made by Company X in horizontal honing machines have significantly enhanced the manufacturing processes across diverse industries. With their unmatched precision, automation capabilities, and versatility, these machines have become invaluable assets for manufacturers seeking to optimize productivity, improve quality, and achieve cost-effectiveness. As manufacturers continue to embrace advanced technologies, horizontal honing machines are expected to play a crucial role in driving innovation and shaping the future of the precision machining industry.
Optimize Engine Performance with Cylinder Liner Honing Tool
Title: Revolutionary Cylinder Liner Honing Tool Revolutionizes Automotive MaintenanceIntroduction:In a game-changing development for the automotive industry, a cutting-edge Cylinder Liner Honing Tool has been launched by a prominent industry player, with the aim of revolutionizing the maintenance and performance of engine components. With its innovative design and advanced features, this state-of-the-art tool promises to enhance efficiency, reduce downtime, and improve the overall durability of engine cylinders, bringing numerous benefits to both car owners and mechanics.Unveiling the Cylinder Liner Honing Tool:Designed and developed by a renowned manufacturer, this recently launched Cylinder Liner Honing Tool brings a new level of precision and quality to the automotive maintenance sector. With its advanced engineering and meticulous attention to detail, this tool delivers unparalleled performance in cylinder honing, providing an effective solution for removing any imperfections or glaze present on engine cylinder walls.Features and Benefits:1. Enhanced Efficiency: The Cylinder Liner Honing Tool adopts an innovative approach to cylinder honing, incorporating cutting-edge technology that significantly reduces honing time without compromising precision. This allows mechanics to complete their tasks swiftly, thereby accelerating the overall repair process and minimizing vehicle downtime.2. Durability and Longevity: Engine cylinder longevity is a critical factor in vehicle performance. By utilizing this revolutionary honing tool, engine cylinders can be honed to perfection, promoting optimal piston and ring sealing. As a result, engine life is prolonged, minimizing maintenance costs and potential breakdowns.3. Improved Performance: The Cylinder Liner Honing Tool ensures that cylinders maintain proper roundness and crosshatch angle, maximizing compression and minimizing oil consumption. This attribute enhances engine performance, leading to increased power output, smoother operation, and reduced emissions.4. Versatile Design: The tool's versatile design caters to various engine models and sizes. This ensures compatibility across a wide range of vehicles, making it an indispensable asset for automotive workshops and professional repair services.5. User-friendly Interface: The Cylinder Liner Honing Tool incorporates user-friendly features, such as intuitive controls and clear visual indicators, enabling mechanics of all skill levels to achieve exceptional results. This ease of use ensures that technicians can quickly adapt to the tool, maximizing productivity and improving overall customer satisfaction.Company Overview:With a rich history spanning several decades, our company has firmly established its position as a leader in automotive manufacturing and engineering. Known for our commitment to innovation and cutting-edge technology, we consistently strive to provide the automotive industry with advanced tools and solutions that meet the evolving demands and challenges of the sector.Our R&D division comprises a team of highly skilled engineers and technicians who work tirelessly to develop groundbreaking solutions. The Cylinder Liner Honing Tool represents the latest milestone in our journey, embodying our dedication to excellence and our continuous pursuit of industry-leading products.Conclusion:The revolutionary Cylinder Liner Honing Tool is set to transform automotive maintenance, offering enhanced efficiency, greater durability, and improved performance. Its advanced features and user-friendly interface make it a valuable asset for mechanics and repair services worldwide. As the automotive industry continues to evolve, this innovative tool ensures that engine cylinders are maintained with exceptional precision and quality, providing car owners with a reliable and high-performing driving experience.