Optimize Your CNC Machine with Precision Honing Tools
By:Admin
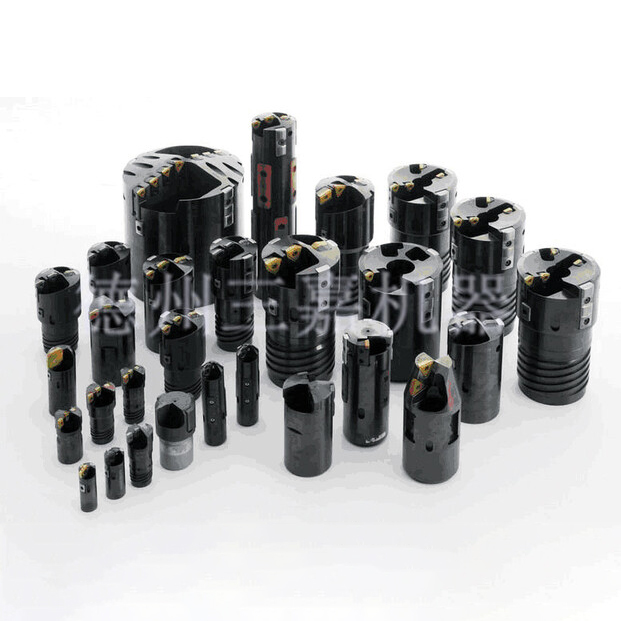
The manufacturing industry has always been at the forefront of innovation and technological advancement. With the rise of CNC (Computer Numerical Control) machines, the demand for precision tools and equipment has increased significantly. One company that has been leading the charge in this arena is {}.
{} has been a pioneer in the design and manufacturing of high-quality honing tools for CNC machines. Their dedication to innovation and their commitment to excellence have made them a trusted partner for companies across a wide range of industries.
The honing process is crucial in the manufacturing of precision components. It involves the use of abrasive stones to improve the geometric form of a surface while also creating the desired finish. However, honing tools must be carefully crafted to ensure optimal performance and accuracy.
{}'s honing tools for CNC machines are designed to meet the highest standards of quality and precision. They are engineered to deliver consistent and reliable results, making them indispensable for manufacturers who value efficiency and excellence.
One of the key features of {}'s honing tools is their advanced design. They are meticulously engineered to deliver superior performance and long-lasting durability. This ensures that they can withstand the rigors of high-speed machining while maintaining their precision and accuracy.
In addition, {}'s honing tools are built with state-of-the-art materials, ensuring that they can handle the most demanding applications. Whether it's a simple bore or a complex surface finishing operation, {}'s honing tools are up to the task.
Another highlight of {}'s honing tools is their versatility. They are suitable for a wide range of materials, including steel, aluminum, and exotic alloys. This makes them an ideal choice for manufacturers who work with diverse materials and need a reliable tool that can handle any challenge.
{}'s honing tools are also known for their ease of use. They are designed to be user-friendly, allowing operators to set them up quickly and get to work with minimal downtime. This not only saves time but also increases productivity, making {}'s honing tools a valuable asset for any manufacturing operation.
Furthermore, {}'s commitment to continuous improvement is evident in their approach to customer support. They provide comprehensive training and technical assistance to help their clients optimize the performance of their honing tools. This hands-on approach sets {} apart from other suppliers and ensures that their customers get the most out of their investment.
With their unwavering dedication to quality and innovation, {} has solidified its position as a trusted partner for manufacturers around the world. Their honing tools for CNC machines have set a new standard for precision and reliability, helping their clients achieve unparalleled levels of productivity and efficiency.
In conclusion, {}'s honing tools for CNC machines represent a breakthrough innovation in the manufacturing industry. With their advanced design, superior performance, and unmatched versatility, they have become an essential asset for companies looking to elevate their capabilities and achieve exceptional results. As the industry continues to evolve, {} remains at the forefront, leading the way with their commitment to excellence and their relentless pursuit of superior quality.
Company News & Blog
Revolutionary BTA Machines: Unlocking New Possibilities for Businesses
[News Title]: Revolutionary BTA Machine Enhances Drilling Accuracy and Efficiency While Minimizing Costs[News Introduction]:In a groundbreaking development that promises to revolutionize the drilling industry, a cutting-edge BTA machine has been introduced by a leading technology company. With a commitment to innovation and efficiency, this company has created a proprietary drilling system that combines high precision and cost-effectiveness. By incorporating advanced technologies, their BTA machine is set to transform drilling operations across various industries, benefiting both operators and clients.[News Body]:Introduction to the BTA Machine:The newly introduced BTA machine is a state-of-the-art drilling system designed to enhance accuracy, performance, and productivity. Built with an unwavering focus on reliability and efficiency, this machine incorporates the latest advancements in drilling technology. Its cutting-edge features ensure precise drilling in a wide range of materials, offering a critical advantage to industries such as aerospace, automotive, energy, and manufacturing.Advanced Technologies Driving Innovation:At the core of this revolutionary BTA machine lies a series of advanced technologies that set it apart from conventional drilling systems. One such technology is the integration of computer numerical control (CNC), which enables operators to program drilling operations with incredible accuracy and customization. The CNC system intelligently adapts to specific drilling requirements, allowing for consistent and repeatable results.In addition, the BTA machine is equipped with a real-time monitoring system that collects and analyzes drilling data. This data-driven approach allows operators to optimize drilling parameters on-the-go, enhancing overall efficiency and reducing material waste. The ability to monitor and adjust various parameters in real-time ensures high-quality and cost-effective drilling operations.Enhancing Accuracy and Efficiency:The BTA machine's advanced features contribute significantly to improving accuracy and efficiency, making it a game-changer in the industry. Its innovative design eliminates the chances of deflection during drilling, resulting in highly precise boreholes. This enhanced accuracy reduces the need for additional machining or post-processing, ultimately saving time and costs for operators.Moreover, the BTA machine's high feed rates and quick tool change capability boost productivity. By significantly reducing cycle times, drilling operations can be completed faster, allowing operators to optimize their production schedules. This increased efficiency not only translates into higher throughput but also enables operators to meet strict project deadlines.Cost-Effectiveness and Sustainability:The introduction of this revolutionary BTA machine also emphasizes cost-effectiveness and sustainability. By minimizing material waste through its precise drilling capabilities, it helps conserve resources while reducing overall manufacturing costs. The machine's real-time monitoring capabilities enable better usage of cutting tools, optimizing their lifespan and reducing the need for unnecessary replacements.Furthermore, the BTA machine's energy-efficient design and reduced environmental impact align with growing sustainability demands. It prioritizes resource efficiency without compromising performance, underscoring the company's commitment to environmentally conscious manufacturing processes.Applications and Industry Impact:The versatile BTA machine caters to a wide array of applications, ranging from deep-hole drilling in aerospace components to automotive engine blocks and hydraulic cylinders. Its ability to drill holes with exceptional accuracy, regardless of materials, makes it an indispensable tool in various industries.The impact of this BTA machine on industries is significant. Aerospace manufacturers can achieve tighter tolerances and reduce costly post-processing operations. Automotive manufacturers can now drill complex engine blocks more accurately, resulting in enhanced reliability and performance. Manufacturers across sectors benefit from the machine's efficiency, allowing them to streamline production and meet increasing market demands.Conclusion:The launch of this cutting-edge BTA machine marks a significant milestone in the drilling industry. With its advanced technologies, unwavering focus on accuracy and efficiency, and commitment to cost-effectiveness, this revolutionary machine is set to transform drilling operations for numerous industries. As the adoption of this BTA machine expands, it is clear that its benefits will have a far-reaching impact, revolutionizing drilling practices and setting new industry standards.
Experts Showcasing Effective Techniques for Deep Hole Drilling
Title: Advancements in Deep Hole Drilling Technologies Revolutionize Industrial ManufacturingIntroduction:Deep hole drilling plays a crucial role in the manufacturing industry by enabling the production of complex components that are essential in various sectors, including aerospace, automotive, and energy. A modern deep hole drilling company, known for its cutting-edge technology and innovative solutions, has recently unveiled its latest advancements that are set to revolutionize industrial manufacturing. This article explores the company's latest deep hole drilling technologies, their applications, and the positive impact they are expected to have on the industry.I. Overview of Deep Hole Drilling:Deep hole drilling is a machining process used to create holes with large depth-to-diameter ratios, typically greater than 10:1. It involves removing material from a workpiece, using specialized tools, while maintaining high precision and surface quality. Deep hole drilling is utilized in a wide range of applications, including manufacturing of oil and gas drill pipes, gun barrels, automotive engine components, and hydraulic cylinders.II. New Deep Hole Drilling Technologies:The recently unveiled deep hole drilling technologies developed by the company mark a significant leap forward in terms of efficiency, precision, and versatility. These advancements include:1. Adaptive Feed Control System:The company has developed an adaptive feed control system that utilizes advanced sensor technology to constantly monitor and adjust the feed rate of the drilling process. This innovative feature ensures optimal drilling conditions, enhancing tool life and reducing cycle times. The system also minimizes vibration and improves chip evacuation, resulting in improved hole quality and enhanced productivity.2. High-Speed Deep Hole Drilling:Incorporating advanced cutting edge technology, the company's latest deep hole drilling machines achieve significantly higher drilling speeds compared to traditional methods. These machines utilize special tool geometries and coatings that improve chip control and heat dissipation, enabling faster material removal rates without compromising on accuracy or surface finish.3. Intelligent Control Software:The company has developed intelligent control software that maximizes productivity and minimizes human error. Equipped with a user-friendly interface, the software offers real-time monitoring of drilling parameters, automated tool wear detection, and predictive maintenance alerts. This technology empowers operators to optimize drilling processes while ensuring consistent quality and reducing downtime.III. Applications and Benefits:The innovative deep hole drilling technologies developed by the company have widespread applications across various industries, offering numerous benefits to manufacturers:1. Aerospace Industry:Deep hole drilling plays a critical role in aerospace manufacturing, where complex components with stringent quality requirements are common. The company's advancements enable faster production of turbine engine components, landing gear parts, and structural elements, while maintaining the highest levels of precision and reliability.2. Automotive Sector:In the automotive industry, deep hole drilling is crucial for manufacturing engine blocks, crankshafts, and connecting rods. The new technologies offer increased productivity, reduced cycle times, and enhanced hole quality, leading to improved engine performance, fuel efficiency, and durability.3. Energy Sector:Deep hole drilling is vital for the production of components used in the energy sector, such as oil and gas exploration tools and nuclear reactor components. The latest technologies enable efficient machining of long and complex parts, improving their reliability and overall performance.IV. Future Prospects and Conclusion:The implementation of these new deep hole drilling technologies not only ensures more efficient and reliable manufacturing processes but also opens up possibilities for the production of previously unattainable components. With its commitment to innovation and relentless pursuit of excellence, the company continues to push the boundaries to meet the evolving needs of the manufacturing industry. These advancements in deep hole drilling underscore their significant contribution to enhancing industrial manufacturing and further cement the company's position as a global leader in the field.
Revolutionary Drilling Tool: Harnessing Advanced Technology for Unmatched Efficiency
Bta Drilling Tool Revolutionizes the Oil and Gas IndustryIn a world where efficiency and precision are paramount, Bta Drilling Tool has emerged as a game-changer in the oil and gas industry. With a firm commitment to innovation and cutting-edge technology, Bta Drilling Tool has revolutionized the way drilling operations are conducted. Their state-of-the-art tools, backed by decades of research and development, have elevated the industry standard to new heights, making drilling processes safer, faster, and more cost-effective.Founded in {year}, Bta Drilling Tool is a leading global provider of drilling equipment and solutions. Their extensive product portfolio caters to a wide range of drilling requirements, including oil and gas exploration, geothermal energy extraction, and mining operations. The company prides itself on its ability to deliver customized drilling solutions tailored to meet the unique needs of each customer, ensuring maximum productivity and efficiency.At the core of Bta Drilling Tool's success lies their steadfast commitment to pushing boundaries and exceeding expectations. Through continuous research and development, their team of experts has been able to develop some of the industry's most advanced drilling tools. From diamond core bits to downhole motors, Bta Drilling Tool has meticulously designed every product to deliver top-notch performance, durability, and reliability.One of the company's groundbreaking achievements is the development of their patented drilling technology known as {technology name}. This innovative technology has redefined the drilling process by significantly reducing drilling time while maintaining precision and accuracy. By optimizing the hydraulic system and improving the efficiency of drilling fluid circulation, Bta Drilling Tool's {technology name} ensures seamless drilling operations, thus saving time and resources for their customers.Moreover, Bta Drilling Tool's commitment to sustainability sets them apart from their competitors. Recognizing the need for environmentally-friendly drilling practices, the company has incorporated several eco-friendly features into their drilling tools. For instance, their advanced filtration systems help minimize the discharge of harmful drilling fluids into the environment, ensuring that natural habitats and water sources remain protected. This dedication to environmental stewardship has earned Bta Drilling Tool a reputation as a socially responsible and sustainable industry leader.Furthermore, Bta Drilling Tool has solidified its position as a global leader through strategic partnerships with major oil and gas companies. By collaborating with industry giants, Bta Drilling Tool gains access to invaluable expertise and resources, enabling them to develop cutting-edge solutions that address the evolving demands of the industry. These partnerships have also facilitated the exchange of knowledge and best practices, resulting in improved drilling techniques and increased operational efficiency.As the demand for energy continues to rise, Bta Drilling Tool remains at the forefront of the industry, constantly innovating and adapting to meet the evolving needs of their customers. With a dedicated team of engineers and technicians, the company is committed to staying ahead of the curve by investing in research and development. This commitment ensures that Bta Drilling Tool's customers always have access to the latest technology and solutions, empowering them to achieve their drilling objectives with utmost precision and efficiency.In conclusion, Bta Drilling Tool has revolutionized the oil and gas industry with its cutting-edge drilling solutions. Through innovative technologies such as {technology name}, the company has transformed the way drilling operations are conducted, making them safer, faster, and more cost-effective. With a commitment to sustainability and strategic partnerships, Bta Drilling Tool continues to lead the way in driving the industry forward. As the energy landscape continues to evolve, Bta Drilling Tool stands ready to meet the challenges and embrace the opportunities that lie ahead.
Advanced High Precision Honing Machine Unveiled in Latest News Update
High Precision Honing Machine Revolutionizes Manufacturing IndustryWith advancements in technology and the rise of automation, the manufacturing industry is constantly evolving to meet the demands of consumers. One particular innovation that is making waves in the industry is the High Precision Honing Machine, a game changer that is set to redefine the way manufacturers approach honing processes.The High Precision Honing Machine, developed by an industry-leading company, is designed to provide a level of accuracy and precision that was previously unattainable. By utilizing state-of-the-art technology, this machine is able to deliver exceptional results, surpassing the limitations of traditional honing methods.Honing is a machining process used to improve the surface finish of components such as cylinders, gears, and bearings. It involves the use of abrasive stones to remove material in a controlled manner. The High Precision Honing Machine takes this process to a whole new level, offering manufacturers unparalleled precision, efficiency, and quality.One of the key features of this machine is its advanced control system, which allows for precise adjustments and measurements during the honing process. The machine utilizes sophisticated sensors and actuators to automatically adjust the honing parameters in real-time, ensuring consistent and accurate results. This level of automation not only saves time but also eliminates human error, resulting in improved productivity and cost-effectiveness for manufacturers.Furthermore, the High Precision Honing Machine incorporates innovative design features that enhance its performance. The machine's rigidity and stability make it capable of handling high-speed honing operations without compromising precision. Its robust construction ensures minimal vibrations and deflections, leading to superior surface finishes and extended tool life. Additionally, the machine is equipped with a user-friendly interface, allowing operators to easily program and monitor the honing process.The benefits of the High Precision Honing Machine extend beyond its technological advancements. By optimizing the honing process, manufacturers can reduce production costs and material waste. The machine's precise control and monitoring system minimize the need for rework or scrapping of components, resulting in significant cost savings. Additionally, the improved efficiency and productivity offered by this machine enable manufacturers to meet tighter deadlines and handle larger workloads.The introduction of the High Precision Honing Machine has already garnered attention from various industries. Companies involved in automotive manufacturing, aerospace engineering, and the production of hydraulic and pneumatic components are particularly interested in this innovative technology. The machine's ability to produce components with exceptional surface finishes and precise tolerances makes it an invaluable asset for these industries, where high quality and precision are crucial.In conclusion, the High Precision Honing Machine is revolutionizing the manufacturing industry by providing unrivaled accuracy, efficiency, and quality in honing processes. With its advanced control system, robust construction, and user-friendly interface, this machine offers manufacturers the opportunity to improve productivity, reduce costs, and meet the demands of ever-evolving markets. As this technology continues to evolve, its potential applications and impact on the industry are boundless.
DIY Cylinder Honing Machine: A Budget-Friendly Option for Engine Maintenance
Home-based mechanics and small engine repair shops have a new tool in their arsenal with the introduction of the Homemade Cylinder Honing Machine, a cost-effective and efficient solution for honing engine cylinders.The Homemade Cylinder Honing Machine is designed and manufactured by an innovative company that specializes in creating practical and affordable tools for mechanics and hobbyists. With a dedication to quality and precision, they have developed a honing machine that can rival professional-grade equipment at a fraction of the cost.This new machine is perfect for small engine repair shops or DIY enthusiasts who want to hone engine cylinders without breaking the bank. It is compact and easy to use, making it a valuable addition to any workshop or garage. The homemade design allows for customization, giving users the ability to modify and improve the machine to suit their specific needs.The Homemade Cylinder Honing Machine is constructed from durable materials, ensuring longevity and reliability. The company takes pride in providing customers with tools that are built to last, and this honing machine is no exception. It is a solid investment for anyone looking to hone engine cylinders on a regular basis.One of the key features of this honing machine is its versatility. It is compatible with a wide range of engine sizes, making it a versatile tool for mechanics who work on various types of engines. Whether it's motorcycles, small cars, or lawnmowers, the Homemade Cylinder Honing Machine can handle the job with ease.Furthermore, the company offers excellent customer support and technical assistance to ensure that customers are able to use the honing machine properly and achieve the best results. They are committed to providing a positive user experience, and that includes offering guidance and advice for novice users.The Homemade Cylinder Honing Machine is also designed with safety in mind. The company understands the importance of protecting users from potential hazards, and they have incorporated safety features into the design of the honing machine. This gives users peace of mind while working with the equipment, knowing that they are protected from harm.In addition to its practicality and affordability, the Homemade Cylinder Honing Machine is also environmentally friendly. It reduces the need for outsourcing cylinder honing work, which can result in lower carbon emissions and fuel consumption. This aligns with the company's commitment to sustainability, making the honing machine a responsible choice for conscientious mechanics and hobbyists.As an added bonus, the company provides a warranty for the Homemade Cylinder Honing Machine, giving customers added assurance that they are investing in a reliable and well-supported tool. This is a strong demonstration of the company's confidence in their product, and it gives customers the confidence to invest in the honing machine without hesitation.Overall, the Homemade Cylinder Honing Machine is a game-changer for small engine repair shops and home-based mechanics. With its affordability, versatility, durability, and commitment to user safety and support, it is a standout tool in the world of engine repair equipment. The company behind this innovative machine has once again proven their dedication to providing practical and affordable tools for mechanics, and the Homemade Cylinder Honing Machine is a testament to their ingenuity and commitment to quality.
Advanced Four-Axis CNC Deep Hole Drilling Machine Unveiled in Latest News
Title: Advanced Four-Axis CNC Deep Hole Drilling Machine Revolutionizes Industrial ManufacturingIntroduction:In recent breakthrough news, a pioneering Four-Axis CNC Deep Hole Drilling Machine has been unveiled by a cutting-edge industrial machinery company. With its innovative design and state-of-the-art technology, this groundbreaking machine promises to revolutionize the manufacturing industry. Leveraging precision engineering and advanced automation, this deep hole drilling machine offers unparalleled efficiency, accuracy, and versatility for a wide range of industrial applications.1. Enhanced Precision and Accuracy:Utilizing advanced four-axis technology, this new CNC deep hole drilling machine pushes the boundaries of precision machining. The intricate drilling process is executed with exceptional accuracy, ensuring optimal performance in demanding industries such as aerospace, automotive, and energy. The machine utilizes high-precision linear guides and spindle drives, resulting in precise and stable drilling operations. This cutting-edge technology reduces human error, enhancing the overall quality of the finished product.2. Unmatched Efficiency:The integration of intuitive software and automation in this Four-Axis CNC Deep Hole Drilling Machine streamlines the manufacturing process, drastically reducing production time. The machine features a user-friendly interface, allowing operators to easily program and control drilling parameters. The advanced automation capabilities enable constant monitoring and adjustment, minimizing downtime and maximizing productivity. This results in improved manufacturing efficiency and reduced costs for businesses.3. Versatility in Machining Applications:The new four-axis CNC deep hole drilling machine caters to a diverse range of industrial applications, thanks to its adaptable nature. From drilling complex parts to creating shallow holes with high precision, this machine can handle a wide variety of materials, including metal, alloy, and composite materials. Additionally, its four-axis capability ensures the machining of complex parts with intricate geometries, expanding its usefulness across different industries.4. Intelligent Cooling System:The CNC deep hole drilling machine incorporates an intelligent cooling system that helps dissipate heat for prolonged operation. This innovative feature prevents component damage caused by overheating, ensuring extended machine life and reducing maintenance and repair costs. The cooling system also enhances the drilling process by efficiently removing chips and debris, maintaining superior drilling performance throughout the operation.5. Commitment to Quality and Reliability:The company behind the Four-Axis CNC Deep Hole Drilling Machine has built credibility and trust through its commitment to delivering high-quality industrial machinery. With years of industry experience, the company prioritizes stringent quality control measures to ensure that their products meet the highest standards. The machine undergoes rigorous testing to guarantee optimum durability, reliability, and customer satisfaction.6. Positive Industry Implications:The introduction of the Four-Axis CNC Deep Hole Drilling Machine provides a transformative solution for various industries. By improving drilling precision, streamlining processes, and reducing production time, this cutting-edge machine enhances manufacturing capabilities, facilitating technological advancements, and ultimately leading to cost-effective and high-quality end products.Conclusion:The unveiling of the Four-Axis CNC Deep Hole Drilling Machine marks a significant milestone in the manufacturing industry. With its enhanced precision, unbeatable efficiency, and versatility in machining applications, this groundbreaking machine holds tremendous potential to revolutionize industrial manufacturing. By combining advanced technology, automation, and a commitment to quality and reliability, the company behind this innovative machinery is poised to make a significant impact in the market, paving the way for future advancements and driving overall industry growth.
Enhance Your Manufacturing Process with Advanced CNC Deep Hole Drilling Techniques
Title: Revolutionary CNC Deep Hole Drilling Technology Sets New Standards in ManufacturingIntroduction:In today's highly competitive manufacturing industry, precision and efficiency hold the key to success. As a pioneer in the field, company {} has unveiled its cutting-edge CNC Deep Hole Drilling technology, which promises to revolutionize the way parts and components are manufactured. By integrating the latest advancements in machining and automation, this groundbreaking solution aims to significantly improve productivity and quality while reducing production costs.1. Challenges in Traditional Deep Hole Drilling Techniques:Traditionally, deep hole drilling has been a labor-intensive and time-consuming process, requiring specialized equipment and skilled operators. Moreover, achieving high levels of precision and surface finish has been a daunting task. These challenges have limited the scalability and efficiency of deep hole drilling, hindering further advancements in the manufacturing industry.2. The Evolution of CNC Deep Hole Drilling:Recognizing the need for a more efficient and precise solution, {} developed the CNC Deep Hole Drilling technology. By leveraging computer numerical control (CNC) systems, this technology streamlines the entire drilling process, enabling faster production cycles and unparalleled accuracy. Whether it's for aerospace, automotive, medical, or mold and die industries, this innovation offers significant benefits to manufacturers globally.3. Unprecedented Precision and Quality:The CNC Deep Hole Drilling technology utilizes advanced sensors and monitoring systems, ensuring the precise measurement of drilling depth, diameter, and surface finish. This level of control enables manufacturers to achieve the tightest tolerances, resulting in parts and components with superior quality. By reducing human error and enhancing repeatability, this technology greatly minimizes the risk of defects, waste, and rework.4. Enhanced Efficiency and Productivity:With its automated features, the CNC Deep Hole Drilling technology optimizes the manufacturing process, eliminating the need for time-consuming manual interventions. The integration of intelligent chip management systems prevents chip accumulation, enhancing drilling efficiency and prolonging tool life. Moreover, the system's ability to perform multiple drilling operations simultaneously reduces cycle times, boosting overall productivity.5. Cost Reduction and Resource Optimization:By maximizing efficiency and minimizing material waste, the CNC Deep Hole Drilling technology leads to significant cost savings for manufacturers. The precise measurement and control of drilling parameters minimize the consumption of feedstock, reducing material costs. Additionally, the integrated coolant systems ensure efficient heat dissipation, preventing tool wear and extending tool life, thereby reducing the need for frequent tool replacements.6. Versatility and Adaptability:One of the key advantages of the CNC Deep Hole Drilling technology is its versatility. The system can handle a wide range of materials, including steels, alloys, composites, and non-metals, adapting to diverse manufacturing requirements. This flexibility allows manufacturers to explore new product designs and expand their offerings, catering to a variety of industries and applications.7. Future Prospects and Market Impact:The introduction of the CNC Deep Hole Drilling technology by {} is expected to have a profound impact on the manufacturing industry. With its advanced capabilities, this solution promises to spur innovation and drive progress in various sectors. The improved precision, efficiency, and cost-effectiveness offered by this technology will enable manufacturers to meet increasing market demands while maintaining a competitive edge.Conclusion:As manufacturing continues to advance, the demand for faster, more accurate, and cost-effective production techniques grows. The CNC Deep Hole Drilling technology introduced by {} sets new standards in precision machining and automation. Its ability to deliver unprecedented precision, enhance efficiency, and reduce costs ensures its crucial role in shaping the future of manufacturing. With this innovative solution, manufacturers can look forward to improved productivity, higher quality parts, and a sustainable competitive advantage.
Efficient Blade Honing Machine for Clippers Enhances Precision and Performance
Title: Revolutionary Clipper Blade Honing Machine Revolutionizes Grooming IndustryIntroduction:In an exciting development for the grooming industry, we introduce a cutting-edge Clipper Blade Honing Machine (name removed) that is set to revolutionize the way professionals and individuals maintain their clipper blades. This state-of-the-art technology is designed to enhance the performance and lifespan of clipper blades, ensuring an unparalleled grooming experience.Company Background:With years of experience in the grooming industry, our company is dedicated to designing innovative solutions that meet the evolving demands of professionals and consumers alike. Our commitment to quality and customer satisfaction has driven us to develop the Clipper Blade Honing Machine, a product that guarantees outstanding results and longevity for clipper blades of all types.1. The Clipper Blade Honing Machine:The Clipper Blade Honing Machine boasts a multitude of features that set it apart from traditional honing methods. This compact and user-friendly device leverages advanced honing technology, combining precision engineering and automation to deliver exceptional results.2. Revolutionary Honing Technology:Utilizing cutting-edge technology, our honing machine employs an intricate system to restore the sharpness and precision of clipper blades efficiently. The machine's honing disk, crafted from high-quality materials, is designed to provide the perfect balance of abrasion and gentleness, ensuring optimal blade performance.3. Unmatched Performance:By employing a combination of honing and gentle polishing actions, the Clipper Blade Honing Machine removes build-up, burrs, and uneven edges, delivering razor-sharp blades with minimal material loss. This process significantly extends the lifespan of the blades, allowing professionals and individuals to achieve consistent, professional-grade results with each use.4. Versatility and Customization:Our Clipper Blade Honing Machine is adaptable to a wide range of clipper blade sizes and brands, making it an invaluable asset for professional groomers, salons, and pet owners alike. The machine also offers customizable honing settings, catering to the specific needs of different blades – from coarse fur to delicate fur, ensuring a tailored grooming experience.5. User-Friendly Interface:Designed with ease of use in mind, the machine features a user-friendly interface that allows for simple operation with minimal training. Equipped with intuitive controls and helpful indicator lights, even novice users can achieve professional-level sharpening results effortlessly.6. Durability and Longevity:Crafted from lightweight and durable materials, the Clipper Blade Honing Machine is built to withstand continuous usage. Its robust construction ensures reliability and longevity, providing a long-term solution for the maintenance of clipper blades.7. Time and Cost Efficiency:With its rapid honing process and high-powered motor, our honing machine reduces honing time by up to 50% compared to manual methods. This not only saves grooming professionals valuable time but also minimizes operational costs while delivering consistent high-quality results.Conclusion:The introduction of our revolutionary Clipper Blade Honing Machine marks a significant milestone in the grooming industry. By combining cutting-edge technology, versatility, and unmatched performance, our honing machine provides an efficient, cost-effective, and user-friendly solution for maintaining clipper blades. Embrace this remarkable innovation and elevate your grooming experience to new heights.
Top-quality Gun Drills for Efficient Lathe Operations
Title: Revolutionary Lathe Gun Drill Redefines Precision Engineering: A Promising Innovation Makes Its DebutIntroduction: [date] - The precision engineering industry welcomes the arrival of a groundbreaking innovation that is set to redefine the way drilling and machining are conducted. Developed by an industry-leading company [], the revolutionary Lathe Gun Drill promises to revolutionize the manufacturing sector by offering unparalleled accuracy, efficiency, and versatility.Paragraph 1: Overview of the Lathe Gun DrillThe Lathe Gun Drill is a versatile drilling machine designed to meet the evolving needs of precision engineering. Built upon cutting-edge technology and innovative engineering, this state-of-the-art equipment offers numerous advantages over traditional drilling methods, including improved accuracy and faster machining speeds. This invention has the potential to transform multiple industries, ranging from automotive to aerospace, and from heavy machinery to medical devices.Paragraph 2: Enhanced PrecisionOne of the key features of the Lathe Gun Drill is its ability to consistently produce precise and accurate holes. Utilizing advanced control systems and precision components, this equipment ensures minimal deviation from the desired dimensions, resulting in high-quality machined parts. The Lathe Gun Drill eliminates the need for multiple tool changes, saving time and significantly reducing the chance of errors. Precision engineering demands perfection, and this innovation sets a new benchmark for achieving it efficiently.Paragraph 3: Unmatched EfficiencyThe Lathe Gun Drill is built to maximize productivity while minimizing downtime. By integrating a streamlined workflow, this groundbreaking machine reduces the need for constant tool adjustment, thereby minimizing production interruptions. Featuring a robust design and high-performance materials, it offers increased durability, reducing maintenance costs and time-consuming repairs.Paragraph 4: Versatility in ManufacturingThe Lathe Gun Drill brings versatility to precision engineering by offering the capability to perform various drilling operations in a single setup. With the ability to drill complex profiles, create intricate patterns, and produce precise chamfers, this innovative equipment eliminates the necessity for additional tools and manual labor. Streamlining the manufacturing process, it not only saves time, but also opens possibilities for designing intricate products that were previously deemed challenging to create.Paragraph 5: Industry ApplicationsThe Lathe Gun Drill has far-reaching implications across a wide range of industries. In the automotive sector, this innovation can be used for engine head and crankshaft drilling, while in aerospace, it offers precision drilling for turbine blades and complex engine components. Moreover, manufacturers in the medical devices domain can leverage its capabilities to create intricate surgical instruments with the highest degree of accuracy.Paragraph 6: Company Introduction and Commitment to Innovation[] is the driving force behind this groundbreaking invention. With a strong heritage in precision engineering and an unwavering commitment to innovation, they have successfully developed an industry-leading solution that has the potential to reshape manufacturing processes worldwide. The company's dedication to research and development, coupled with its extensive expertise, ensures that they continue to push the boundaries of technological advancements in the precision engineering field.Conclusion:The introduction of the Lathe Gun Drill marks a significant milestone in precision engineering, promising enhanced precision, unmatched efficiency, and unrivaled versatility. As this groundbreaking innovation makes its debut in the market, manufacturers across various industries can look forward to a transformative upgrade in their machining capabilities. With its potential to revolutionize the manufacturing sector, the Lathe Gun Drill represents a remarkable leap forward in precision engineering.
Gun Drilling on a Lathe: Techniques, Benefits, and Applications
Gun Drilling on A Lathe: Revolutionizing Precision Machining Precision machining has always been a crucial aspect of manufacturing industries, requiring innovative techniques and cutting-edge technologies to meet the highest standards of accuracy and efficiency. Among the many advanced technologies employed in precision machining, gun drilling on a lathe has emerged as a game-changer, providing unparalleled precision and versatility for machining applications. This revolutionary method, which has rapidly gained popularity in recent years, is making waves in industries ranging from aerospace to medical equipment manufacturing. At the forefront of this cutting-edge technology is a leading manufacturer that has been pioneering the development and implementation of gun drilling on a lathe. With a rich history dating back several decades, the company has become synonymous with quality, innovation, and reliability. Through a relentless pursuit of excellence, they have solidified their position as a trusted provider of precision machining solutions globally.Gun drilling on a lathe represents a significant breakthrough in the realm of precision drilling. Traditionally, gun drilling involved the use of specialized machinery, separate from lathes, to create deep, straight holes with a high degree of accuracy. However, the integration of gun drilling capabilities into lathes has revolutionized the machining process by eliminating the need for additional equipment, reducing setup time, and streamlining operations.The key advantage of gun drilling on a lathe lies in its ability to create deep holes with a diameter-to-depth ratio that was previously unachievable. By employing a single-lip drill bit with a coolant system, chips are efficiently flushed away from the cutting area, ensuring precise and clean drilling. This technique enables manufacturers to produce complex components with deep holes, such as gun barrels, hydraulic cylinders, and molds, to name a few.The incorporation of gun drilling on a lathe has also brought about significant enhancements in productivity and efficiency. The integration of this technique into the lathe eliminates the need for transferring workpieces between different machines, reducing the risk of dimensional errors and minimizing downtime. This seamless integration not only saves time but also allows for better control over the machining process, resulting in superior surface finishes and tighter tolerances.Moreover, the company's commitment to innovation and continuous improvement is evident in their investment in advanced technologies to enhance gun drilling on a lathe. State-of-the-art control systems and software have been integrated into their lathes, providing unmatched precision, repeatability, and flexibility. These advancements enable manufacturers to meet the ever-increasing demands for intricate and complex machined components with unparalleled accuracy.Gun drilling on a lathe is transforming various industries, particularly aerospace and medical equipment manufacturing. In aerospace applications, where lightweight and durable components are crucial, this technology enables the production of turbine blades, fuel nozzles, and engine components with intricate cooling channels and improved performance. Similarly, in the medical field, gun drilling on a lathe is employed to manufacture surgical instruments, implantable devices, and prosthetics, where precision and reliability are of utmost importance.Furthermore, environmental considerations have also played a significant role in the adoption of gun drilling on a lathe. The coolant systems employed in this method ensure minimal waste generation, reducing both environmental impact and operational costs. Additionally, the use of specialized coatings and materials improves the lifespan of the drill bits, reducing the frequency of tool changes and enhancing sustainability.As industries increasingly demand higher precision and efficiency, gun drilling on a lathe is set to play an indispensable role in the future of precision machining. With its ability to create deep and complex holes with unmatched accuracy and efficiency, this technology opens up new possibilities for engineers and manufacturers across a wide range of industries. The company's relentless commitment to innovation and the continuous refinement of gun drilling on a lathe ensures that they remain at the forefront of providing cutting-edge solutions to meet the evolving needs of their customers.In conclusion, gun drilling on a lathe represents a groundbreaking advancement in precision machining, revolutionizing the manufacturing industry. By seamlessly integrating gun drilling capabilities into lathes, this technology offers unparalleled accuracy, productivity, and versatility. With its extensive history of innovation and commitment to excellence, the company continues to drive the adoption and advancement of gun drilling on a lathe, empowering manufacturers around the world to achieve new levels of precision and efficiency.